“Only good work leads to doing more good work”
Michael Bierut
A work management framework consists of Identifying, Planning, Scheduling, Executing and Completing work. Anybody and everybody can have this framework within their organisation, however, what are some of the things that need to be considered in each of these process areas to make this framework… good?
Let’s look at each of the process steps in turn, highlighting some key points.
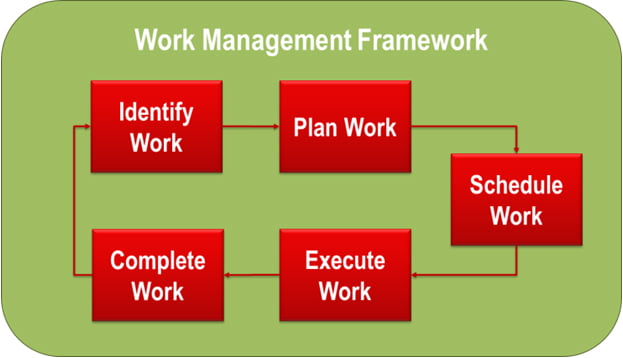
Step 1: Identifying the work
In addition to Preventive Maintenance work orders which will be generated automatically as a Forward Log by your CMMS at required intervals, maintenance personnel will also be required undertake work of a corrective nature on equipment that has failed or is about to fail. This corrective work is identified as either Breakdown Maintenance, ie. fix it ASAP, or Scheduled Corrective Maintenance, ie. plan and schedule the repair. Corrective work identified as Breakdown Maintenance (BM) is pretty obvious as the equipment has failed and the consequences generally have a major impact upon safety, environment and/or operations. BM usually has some impact on the conduct of PMs as limited resources available for maintenance will generally be taken away from the PM activities to undertake BM activities.
However, identification of Scheduled Corrective Maintenance is an area that is sometimes not that obvious and if not properly managed, can lead to waste. Waste not only in the time and efforts of personnel but also the lost opportunity in terms of cost, resources and consequence of making a small repair to equipment before it fails. Or if the equipment has already failed, making the repair before other subsequent events occur that lead to significant consequences in terms of safety, environment and/or operations, ie. ‘a stitch in time saves nine’. A good example of this is with redundant systems. The following are some of the key ways in which you can make Identifying Work good:
- Empower all personnel with the responsibility to be able to identify and communicate potential corrective work. Identification of potential corrective work is the responsibility of all, not just the maintenance staff.
- There must be clear methods in place for the identified potential work to recorded and communicated to planners. This may be through some form Work Notification/Request on your CMMS or perhaps through a log book in a small/simple CMSS organisation.
- Train personnel to not only be able to identify, record and communicate the potential corrective work (in your CMMS), but also ensure that they include a clear and concise description of the equipment, its location, the problem encountered, and avoid attempts to provide a fix to the problem. Descriptions in vague and general terms don’t help planners identify the problem and suggested fixes may only address the symptoms and not the actual problem. Both of these can lead to time being wasted for the planner to try to both understand the real problem and the required solution.
- Work Notifications/Requests must be screened regularly (daily at minimum) to:
- Ensure potential problems are not ignored, especially those where the consequences of failure could be significant if not addressed in a timely manner.
- Make sure that the information is complete and accurate to allow a decision to be made on the significance of the identified problem.
- Make sure that only ‘real’ problems are converted into Work Orders.
- Allow an appropriate priority for undertaking the work to be determined based upon risk (likelihood and consequence). This will then generate a prioritised backlog list of work orders, eg. Essential, highly desirable, desirable, that then forms an input for consideration into scheduling of work. This prioritisation must be down as a partnership between operations/production and maintenance.
- To minimise the chances of duplicate work orders being raised.
- Provide feedback to the originator as to why a Work Notification/Request has not proceeded to a Work Order. This communication shows the originator that they have been heard, the issue considered and a decision made with reasons. This communication is important for ensuring personnel don’t feel they are being ignored and that they continue to sustain their efforts in identifying potential corrective work.
Step 2: Planning the work
Now that the work has been identified and prioritised, the work must be planned. Proper planning of scheduled work, whether preventive or corrective, will answer the questions:
- How long the job will take?
- How much and of what types of labour will be required?
- What parts and materials will be required? This will then allow parts to be ordered and the work to be scheduled to align with the delivery of those parts.
- What tools, equipment or other resources, including external contractors, will be required?
- What permits will be required?
- What are the job hazards and how will they be managed them?
Answering these questions should lead to the creation of good quality work packs that are sustainable and reusable. Good work packs ensure time is not wasted from the actual execution of the task. Creating a library of work packs for repeatable tasks, both preventive and key corrective tasks, will also minimise the time required for planning the next time the task comes around. Proper planning is a key part of efficient and effective execution of the work.
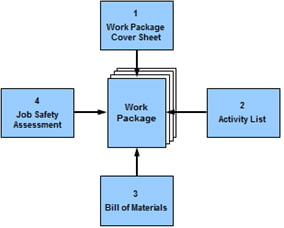
Proper planning of the right work will then contribute to minimising the impact of maintenance on operations through:
- Less unscheduled downtime – more uptime.
- More warning of required downtime to be scheduled – perhaps reducing consequences of downtime and allow contingencies to be planned for the period.
- Ensuring effective and efficient use of resources – the time of personnel is not wasted.
Step 3: Scheduling the work
The important part of scheduling is to attempt to ensure the work that is scheduled for a particular timeframe, is actually completed within that timeframe. If it isn’t, then it will return to the backlog to be rescheduled for another time. This means more work. Hence if it is scheduled, ideally you want it completed. Naturally there may be circumstances that prevent the ideal from happening, however, here are some tips to maximising scheduling success:
- Ensure the work pack, permits, spares, tools and other resources are all available and ready before the work actually starts.
- Include contingency for breakdowns. The best PM program in the world won’t stop all unscheduled failures from occurring. All equipment will fail in some way at some time and if the failure pattern for the equipment is random, you won’t know when. Consequently with limited workforce numbers and hours in a tradespersons shift, not all of the tradespersons hours should allocated to scheduled work. A good rule of thumb is to allocate around 80% of the tradespersons time to scheduled work in a shift. The remaining 20% of time in the shift covers any administration and contingency for any breakdown maintenance required.
- Balance the scheduled work. With 80% of the shift allocated to scheduled work, not all the work scheduled should be the essential high priority work. A balance of prioritised planned work should be scheduled within the shift. For example, for the available scheduled work hours in the shift, a balance of 60% essential work, 20% highly desirable and 20% that could be postponed with no significant consequences (…yet). Undertaking this balance of prioritised work achieves three objectives:
- It ensures that a number of the mid to lower priority planned tasks are carried out in a timely manner…before they in turn perhaps become high priority tasks requiring perhaps breakdown maintenance action.
- Demonstrates and provides confidence to staff that something is being done about lower level priority tasks. This encourages continual reporting of problems, not just those perceived as high priority.
- Provides an additional buffer for any breakdown maintenance which may take more time than the original 20% contingency already factored into the shift. In this scenario, the aim is that if the breakdown intrudes upon the time allocated for the ‘postpone able’ or possibly even the highly desirable tasks, at least the essential tasks have been completed and the residual risk to the equipment when released back to operations is minimised.
Step 4: Executing the work
‘To err is human’ and ‘nobody’s perfect’. As humans, regardless of whatever field, we all make errors. However, through design of systems, both physical and procedural, what we try to do is make it hard for personnel to do the wrong thing and easy for them to do the right thing. When it comes to minimising errors in executing the work, and thereby minimising waste subsequently introduced from early failures and/or rework, the following steps should be undertaken:
- Ensure personnel have been appropriately trained and are assessed as competent to undertake the task.
- For key critical tasks, incorporate additional work completion checks by supervisors or independent assessors to be undertaken to ensure the work has been done right.
- Ensure Supervisors periodically check out the progress of their teams throughout the day. Supervisors are called supervisors for a reason.
- Create high quality work instructions that are clear and concise. Remove any potential ambiguity or confusion in what needs to be performed. These instructions ideally should define to what standard the work needs to be performed and what needs to be done if the standard is not met. Once created, these instructions need to be configuration controlled and included as part of the work pack for the relevant maintenance activity.
Step 5: Completing the work
The final step is making sure that when the work is complete, work orders record all the relevant information that is necessary to support your organisations’ needs and objectives. Generally the reasons we need to accurately record this history is to capture costs, support failure analysis, support performance improvements and support continuous improvement of the work management system, including the tasks and associated work instructions. The accuracy and depth of this information to support these analyses can then help to improve equipment reliability (reducing unscheduled maintenance), improve task time accuracy for planning purposes, and improve the quality and accuracy of work instructions. If the accuracy and depth of information recorded in the completed work order is not there to support our needs and objectives, then any efforts at improvements will be difficult if not impossible.
Work we have undertaken with our clients indicate that a properly structured, controlled and sustained work management system is vital to the success of improving workforce productivity, equipment uptime and reducing maintenance costs (through less unscheduled maintenance). In work we did for an onshore gas operation client, developing and implementing improved standardised work management processes, we saw an improvement in adherence and sustainment to procedures and processes, and a resultant increase in scheduled work compliance in the order of 30% over a period of a year. Improvements still needed to be made but were being worked on to achieve world benchmark levels. In addition the client also saw a reduction in the quantity of unscheduled work occurred over the period. These are the types of benefits any organisation can have with a good work management framework.
If you enjoyed this article and want to receive notifications of future articles that we publish, please sign up for our newsletter here.