In the first in this series of articles, we discussed the benefits that leading organisations enjoy when they have high levels of maintenance productivity, and outlined five ways in which maintenance productivity may be improved. These were:
- Doing the right work
- Doing the work right
- Focusing on continuous improvement
- Creating an environment for success
- Thinking holistically
In this article, we will tackle the first of these 5 keys to Lean Maintenance and Maintenance Productivity Improvement.
As we stated in 5 Keys to Lean Maintenance and Improving Maintenance Productivity, doing work for work’s sake is simply a waste of time and resources – yet in our experience, there are primarily two ways in which organisations most commonly waste their tradespeople’s time by generating unnecessary work:
- Having inappropriate Preventive Maintenance programs
- Doing low (or even no) priority jobs
How does the waste in your preventive maintenance program occur?
In organisations with fully mature Preventive Maintenance programs, there can often be opportunities to reduce the amount of tradesman time spent on performing Preventive and Predictive maintenance by up to 50%, while simultaneously improving plant performance and reliability. How can this be?
The reasons are many, and may include some or all of the following:
- Initial PM programs may have been set up when the plant was first commissioned, and at that time there was limited understanding of how often the plant would fail, and what the causes of those failures would be. As a result the PM program that was put in place was a “best guess” at the time, but has never been reviewed since.
- Plant failures may have occurred, but the causes of those failures may not have been fully investigated and understood. Nevertheless, in reaction to those failures, additional (unnecessary or inappropriate) PM activities may have been established, or the frequency with which PM tasks are performed may have (inappropriately) been increased.
- There may be a bias towards favouring fixed interval replacement or overhaul of equipment, when a condition-based approach may be more cost-effective. This can occur for a number of reasons, including:
- Insufficient consideration or analysis having been given to the condition-based alternative (“we have always done it this way”)
- A desire for greater “certainty” regarding the timing of equipment overhaul or replacement activities and their associated costs. (Note that this “certainty”, even if true, comes at an additional cost, the size of which is often not understood)
- Lack of awareness of the full range of condition monitoring technologies, and their capabilities
- The operating requirements may have changed over time (increases or decreases in required uptime and throughput, or changes in the composition of materials being processed), but the PM program may not have been updated in line with these new requirements
- The opportunity cost of lost production may have changed over time (increased as product prices have increased, or decreased as product prices have decreased) therefore changing the cost-effectiveness of some PM tasks
- The equipment or its components may have been modified and the PM program may not have been updated to take account of these changes.
- PM tasks being done that add no value – they do not reduce the probability of equipment failure, but just add unnecessary cost.
- PM tasks being done at the incorrect frequency – either too frequently (which represents a waste of maintenance labour) or not frequently enough (which increases the risk of equipment failures, and additional unplanned maintenance work to repair those failures)
- Duplicate PM tasks – the same, or essentially the same tasks being done by different work groups (e.g. Mechanical trades, Electrical Trades, Operators) to prevent the same failures. Of these, by far the greatest opportunity for improvement is in reducing the duplication of operator and maintenance inspections. At many organisations, operator inspections are determined independently of the maintenance inspections, and are often developed with a minimum of science or analysis.
- Inappropriate PM tasks types being used (e.g. fixed interval replacements, when condition-based replacement is a more cost-effective alternative, or vice versa).
- Failures occurring which could be prevented with appropriate PM tasks, but these PM tasks have not been established.
For all of these reasons, ongoing review and continuous improvement of the PM program is necessary – but few organisations, in our experience, do this well. The wastes that we frequently see in suboptimal Preventive Maintenance programs include:
The net result of this is illustrated in the figure below; too much PM, as well as too many equipment failures – both of which result in low maintenance productivity.
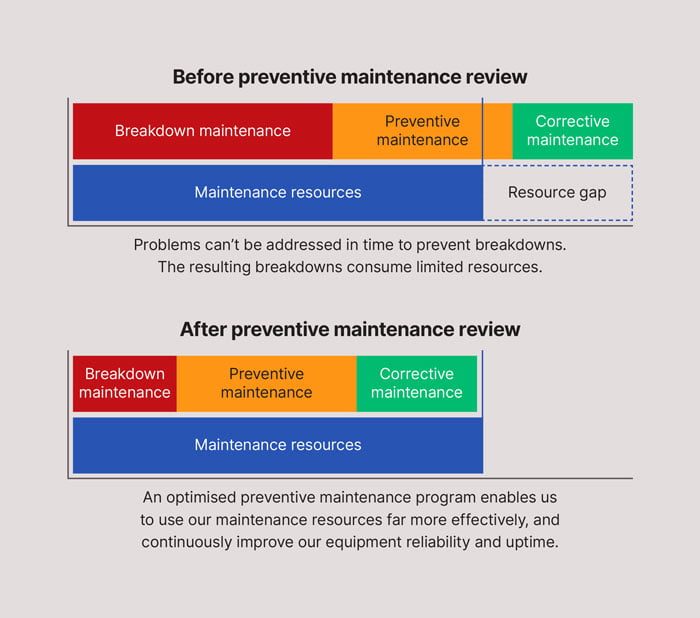
How do you remove the waste in your preventive maintenance program?
There are fundamentally two types of waste that are associated with your Preventive Maintenance program:
- The waste that is embedded in your Preventive Maintenance program, including:
- Unnecessary work
- Duplication of work
- Rework as a result of inconsistent execution of your Preventive Maintenance activities
- The waste that is associated with the process that you use for developing, reviewing and improving your Preventive Maintenance program
In order to address the first of these wastes, there are four fundamental concepts which underpin the development of a successful and waste-free Preventive Maintenance program. These are discussed in our article RCM, PMO and Preventive Maintenance Programs: 4 Key Concepts In addition, there are a range of alternative approaches that can be used to develop and review Preventive Maintenance programs. These alternatives, and their comparative strengths and weaknesses are discussed in our article Alternative Approaches for Developing and Optimising Preventive Maintenance Programs
The key message from both of these articles is that effective optimisation of your Preventive Maintenance program requires a solid foundation in sound engineering principles, and that it will take more than a little effort. There is definitely more work involved in optimising your preventive maintenance program than just cutting and pasting tasks from the equipment manufacturer’s maintenance manual. It may be more work than your current reliability improvement team have time to perform effectively, and so you may require some external assistance. But the key is to ensure that you don’t spend more time than is absolutely necessary to achieve the resulting improvements in Maintenance Labour Productivity and equipment reliability – otherwise this, of itself, represents a waste that should be eliminated. It is important to have a business focus, rather than a technical one, when developing and implementing a PM review process. The key is to be practical, and keep a clear eye on the outcome that you are trying to achieve. Apply a level of rigour in analysis that is commensurate with the level of risk that you are trying to avoid, or benefit that you are trying to gain.
Work that we have done with our clients has indicated that reviewing existing Preventive Maintenance programs using the principles outlined in our article RCM, PMO and Preventive Maintenance Programs: 4 Key Concepts can result in reductions in Preventive Maintenance workload of up to 50%, while simultaneously improving equipment reliability and reducing the amount of maintenance time spent on breakdowns. And this can all be done in a highly cost-effective manner, if the appropriate analysis techniques are chosen, as discussed in in our article Alternative Approaches for Developing and Optimising Preventive Maintenance Programs As an example, the following chart shows the results of a PM program review that we undertook at an Aluminium smelter:
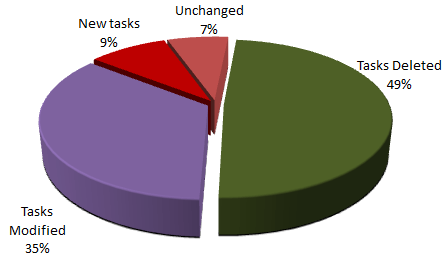
“Doing the Right Work” is clearly a vital part of ensuring that our maintenance workforce is productive. In this article we have focused on the importance of having an optimal Preventive Maintenance program in place, and the impact that this has on maintenance productivity. In the context of Lean Maintenance, improving the quality of your Preventive Maintenance program using some of the techniques and principles outlined in this article will assist you to the eliminate the following wastes:
- Unproductive work – doing work that doesn’t need to be done. This includes:
- Duplication of tasks by different workgroups (Operators, Mechanical Maintenance, Electrical Maintenance etc.)
- Removing tasks that serve no useful purpose
- Reducing the frequency of tasks where these tasks do not need to be done as frequently
- Rework – having to repeat Preventive Maintenance tasks as a result of vague or incomplete descriptions of the Preventive Maintenance tasks required.
- Avoidable Work – having to repair equipment that has failed, when those failures could have been avoided if the correct Preventive Maintenance program had been in place.
In the next article in this series, we will discuss how to put in place effective Maintenance Work Management processes to ensure that you are “Doing the Work Right”, and in doing will also touch on another aspect of “Doing the Right Work” – how to avoid doing low (or even no) priority jobs.
Do you need a more effective preventive maintenance program?
We have over 21 years of experience in improving maintenance programs for a wide range of industries. Our services are catered to your specific business and operational goals, and we aim to be proactive in delivering solutions that are grounded in practicality and bottom-line results. Sound good to you?