When you are in the reactive maintenance “death spiral”, it takes a major change of approach to break out of it.
When I started my career in fixed plant maintenance, I had the great experience of working for 4 years at a gold mine in Tajikistan, Central Asia. At the time the price of gold was about $253 USD an ounce, the head grade was 0.5g per ton.
We were looking down the barrel of a gun with regards to profitability. The pressure was extreme. The mine was completely isolated – no local industries had any ability to support the mine.
Whilst the mine was making no money, it was being severely hampered by the lack of any system to support maintenance.
Shutdown meetings were held, the jobs we would try to complete were discussed, but no one got anything to refer to on the day, spares were difficult to obtain, and the previous 8 years maintenance history was stored in 8 diaries which my predecessor swore were as valuable as the gold bars we were making – “Umm, which page did that breakdown occur on?”
Satellite stores were at the plant, no-one had any record as to what was held in them.
A brilliant place to learn how to respond to breakdowns; but maintenance could have been improved so much by the introduction and use of proper procedures and reliability practices.
When critical spares become truly critical
One breakdown saw me searching through the local market to see if any of the components we needed were being sold, having been previously removed from the mine-site.
To “hotshot” a replacement component took around 6 weeks. If you were lucky, someone may be travelling in from London and smaller parts could be brought in their luggage, but usually, 6 weeks. Normal delivery time was in the order of 6 months.
This meant critical spares became truly critical, worn-out parts got a new lease of life, “It’s not too badly worn, it will run again,” was the normal response to the question, “Have we got a new X, Y, Z component?”
It was not uncommon to see maintenance guys searching the boneyard for jaw crusher wear liners to see if a few more weeks wear could be eeked out of them, or if used pump impellers had any life left in them.
Critical spares became more and more critical, and best practice maintenance became more and more important, but harder and harder to achieve.
The risks of choosing a “quick fix”
One system became a huge issue. The electrowinning/elution circuit. The elution circuit was pretty simple; a couple of pumps, some valves, a heat exchanger, an electric heater and an electrowinning cell.
One of the pumps, the “elution pump”, fed the eluate (a mix of cyanide, caustic and water with microscopic particles of gold held in suspension) from the electrowinning cell through the heat exchanger and back into the cell.
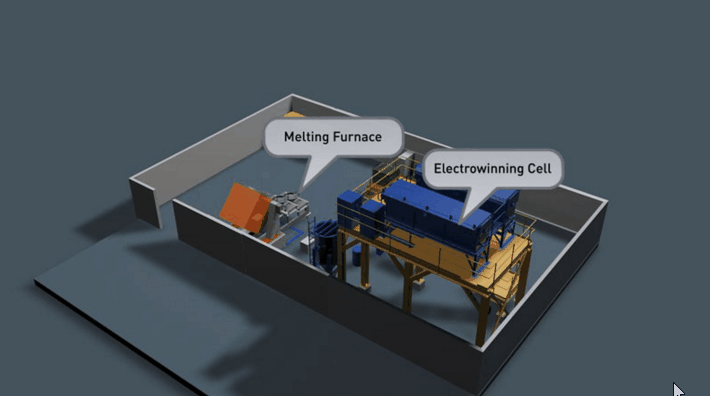
Absolutely critical to the elution circuit, this pump had an mean time between failures (MBTF) of around 2 weeks. When the pump failed, it was all hands-on deck to fix it.
The usual failure was due to the mechanical seal smashing, causing the shaft to rotate unsupported and gouge pieces out of itself (usually where the mechanical seal sat) on the pump casing.
The “quick fix” was to replace the mechanical seal and the shaft. New replacement shafts and seals would be out of stock in a few weeks, with the 6-week wait for new ones to arrive. Often, the “quick fix” took a few days to achieve a seal.
However, the “quick fix” was the norm, not a way to get the pump through to a planned shutdown.
We wasted many hours carrying out a repair that was destined to fail, because the “quick fix” did not deal with the root cause of the issue, it dealt with a symptom of a much bigger failure, but we were in reactive maintenance mode and we were good at it.
My boss at the time decided that the issue was the pump, so, he ordered a new one. After a few weeks of arguing that the pump was not the issue, I was instructed to install the new one.
It managed to survive an hour into an 8 hour “strip” before its mechanical seal failed.
When the pump was ordered, the ability of the pump (specifically the seal) to handle 140°C eluate was overlooked.
140°C melted the rubber seal components, making the pump look like a lawn sprinkler system. The old pump had to be refitted, due to no mechanical seals having been bought for the new pump (not that it would have mattered).
Over time, the reliability of the original pump improved slightly, but failures were still too frequent.
During one such failure I noticed some PTFE-like plastic pieces were inside the pump. This plastic was the liner from the cell. This was getting into the pump, causing it to cavitate.
When it cavitated, the mechanical seal would shatter, causing the shaft to damage itself on its casing, eating our spares and our time.
The simple solution was to fit a strainer on the suction of the pump, capturing any solids that would cause the pump to cavitate. Once fitted, the MTBF increased to in excess of 6 months.
There was no CMMS, no reliability engineer, no planners, no maintenance engineer (no engineer at all!), no RCA, no maintenance plans or inspections.
Each day, the maintenance team were dealing with on average 9 breakdowns (not all production critical), the crew was burned out, the equipment was on the verge of having a mushroom cloud appearing over it at any time.
Are you stuck in the reactive maintenance “death spiral”?
It’s not uncommon for fixed plants to require assistance in breaking out of the reactive maintenance “death spiral.” If the issues discussed in this article are familiar to you, it may be beneficial to explore your options to break the cycle.
As specialist maintenance, reliability and asset management consultants, we would be happy to discuss your specific challenges and help you to create a plan of attack. For more information, view our service pages below or send us a message.
References
1. 911 Metallurgist. “AARL Carbon Stripping System Operation: Elution & Electrowinning”. https://www.911metallurgist.com/blog/carbon-stripping-system-operation. Accessed 16 Nov 2021.