Many companies measure and understand productivity when applied to the creation of the product or delivery of the service they provide – it’s the ratio between output and input. This is a measure of the efficiency with which we use scarce resources – we’re asking “how much wasted time, energy and material goes into making product X or delivering service Y?”
What many asset intensive companies do not measure or understand is that the principles associated with measuring productivity can be applied internally and particularly to their maintenance programs – after all, maintenance is a service. When maintenance productivity is optimised, asset intensive companies often realise a significant commercial advantage over their less effective competitors. Recent studies in a number of asset intensive industries have demonstrated that maintenance “tool time” (actual time doing beneficial maintenance on the asset) can be as low as 20% of the total time “doing maintenance”. By comparison, those that are doing things right are achieving maintenance “tool time” as high as 55-65% . This gives the successful companies a massive competitive advantage by allowing them to operate with much smaller maintenance workforces – potentially as much as one-third of the size of less efficient organisations.
This is the first in a series of 6 articles on improving Maintenance Productivity through the use of Lean Maintenance techniques.
Reduce your costs by 25%
Successfully applying Lean Maintenance techniques may allow you to reduce your maintenance costs by more than 50% (for example, by increasing tool time from 30% to 60%). If Maintenance costs account for 50% of the total cash costs of production (as is the case in some industries), the opportunity may exist to reduce total costs by more than 25% with no adverse impact on equipment performance. This makes it simply too important an opportunity to ignore.
If you haven’t already, maybe now would be a good time to assess your maintenance “tool time” vs total maintenance time. How well are you delivering the maintenance service? If you find you’re in the bottom part of the range, here are 5 key techniques you can try to catch a break on your competitors:
1. Do the right work
Doing work for work’s sake is simply a waste of time and resources – and can even be counterproductive in terms of equipment reliability. Every maintenance task needs to be directly aimed at creating the best “value” from the assets. So how do we select which work we do and to what level of detail? The key to achieving this holistically is to use the principles of Reliability Centered Maintenance (RCM), an extension of Failure Modes and Effect Analysis (FMEA), to identify the right work, at the right frequency, to manage the risk of failure.
Compare the two situations illustrated below. Prior to reviewing its preventive maintenance, the organisation is swamped with breakdown work, which is inherently poorly planned and inefficient, because the wrong preventive maintenance can’t prevent failures. After an appropriate review, the organisation has identified the necessary preventive maintenance, which can be executed efficiently to reduce the breakdown downtime leaving the maintenance workforce with the correct amount of work, and possibly the opportunity for some improvement initiatives. And don’t forget – optimising the maintenance program should not be seen as a “set and forget” – reviews should take place regularly, and especially when things change.
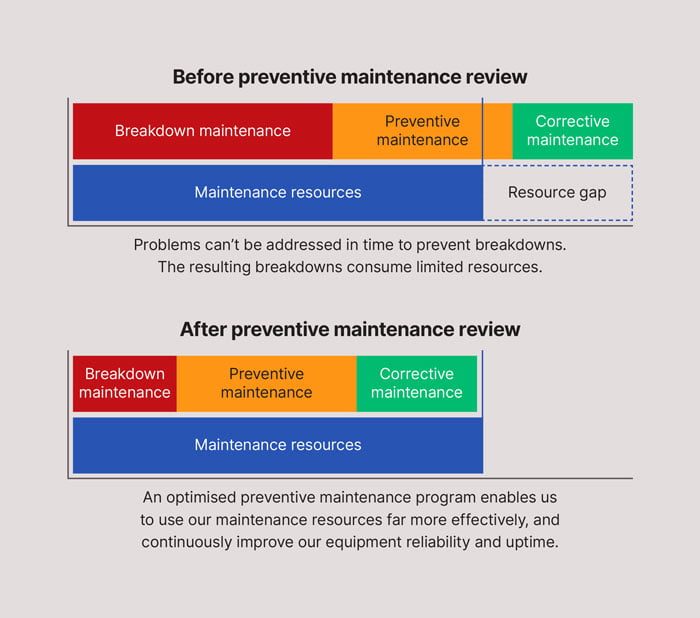
2. Do the work right
Once we’ve established a maintenance program with the right work, what’s next? To get the best from limited resources, the work needs to be executed efficiently and effectively. The key to this is the application of a rigorous Work Management process, as illustrated below:
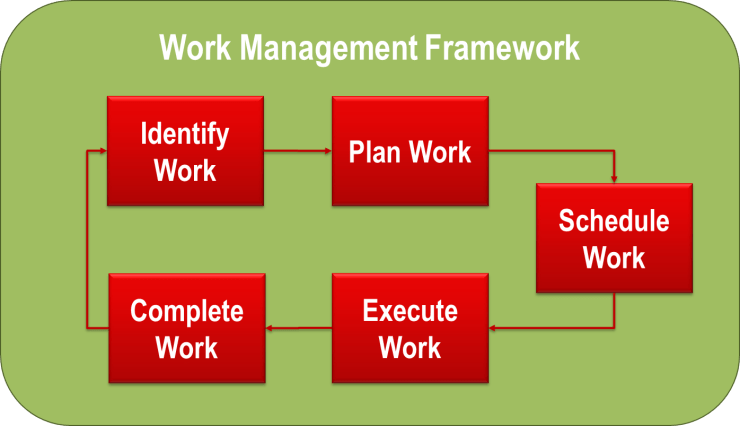
Without these processes in place, maintenance staff waste time and effort on discovering what they should be doing, prioritising tasks, identifying resources (tools, parts, people) required, working out when work can be done, waiting, travelling; all time that could be used for “real” maintenance activities!
Associated with doing the work right is applying effort to reduce the maintenance error rate – getting rid of rework. The Work management process is more than just a routine scheduling process – it includes asking the question “how can I make it more likely that work will be done right?” Focussing on areas such as better planning and scheduling methodology, more detailed and accurate work instructions and better trained maintenance crews are major areas of improvement.
3. Implement continuous improvement
Steps 1 & 2 only take productivity improvement so far – further tools are needed to identify and eliminate causes of issues such as equipment failures, service overruns, lack of required resources and poor schedule adherence. Reducing or eliminating these issues will generate increased plant uptime and throughput, reduced risk of safety and environmental incidents, increased equipment reliability, increased proportion of planned maintenance work, reduced maintenance and operating costs.
But don’t just focus on coming up to a standard – look at the standard itself! You should know what maintenance needs to be done if everything was perfect. But can you change that? Effort applied in areas such as asset design changes, maintenance process changes, converting “off line” maintenance to “on line” maintenance, application of new/different technology and similar often has a dramatic effect on the amount and type of maintenance that needs to be provided.
The following diagram shows a simplified view of a suitable continuous improvement/defect elimination process. This needs to be supported by an appropriate set of formal root cause analysis tools, such as “5 whys”, cause and effect trees and fishbone diagrams.
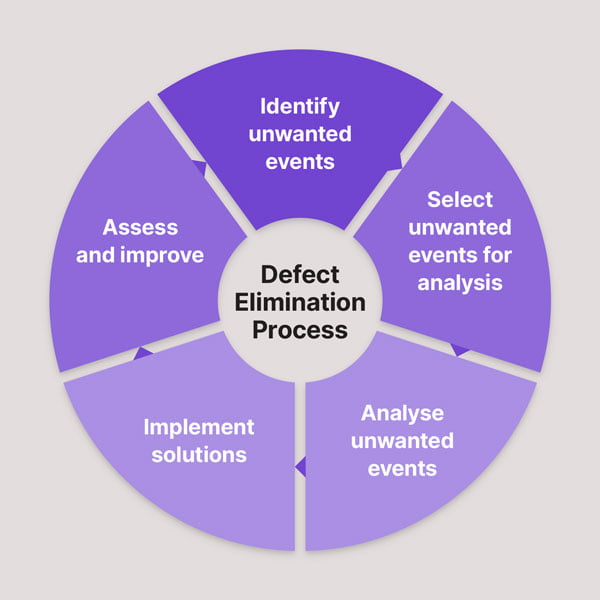
4. Create the environment for success
Any improvement process is headed for failure without the buy-in and support of all those involved; it is imperative that the leadership and culture is focussed on being proactive rather than reactive, and is performance driven. This is an area which many people involved in maintenance miss, due to a natural bias towards technical processes.
The development and implementation of a ‘balanced scorecard’ of Key Performance Indicators (KPIs) and the support and communication from management are the keys to delivering improvement. A real benefit is when the maintenance manager/superintendent can “guard” the maintenance teams, keeping the non-value added, time consuming activities to a minimum, allowing the maintainers to maintain.
5. Think holistically
The Maintenance department and maintenance service it provides don’t exist in isolation to the rest of the business – it is part of a system. So what are your enablers to the Maintenance department and performance of the service? It is not unusual for organisations to focus on one or the other, but not both. The service requires the right people, tools, information and spares at the right place and right time – the department needs the right corporate policies and processes, funding, people, tools, facilities, data and performance measuring. The key to addressing both is fostering good interdepartmental relationships between Maintenance and other areas such as supply, operations, training and human resources. Alignment of departmental scorecards and meetings with attendance from the various departments will assist with achieving the holistic approach required. This type of engagement is fundamental to the discipline of Asset Management, and is a core element of the recently released international standard ISO 55001.
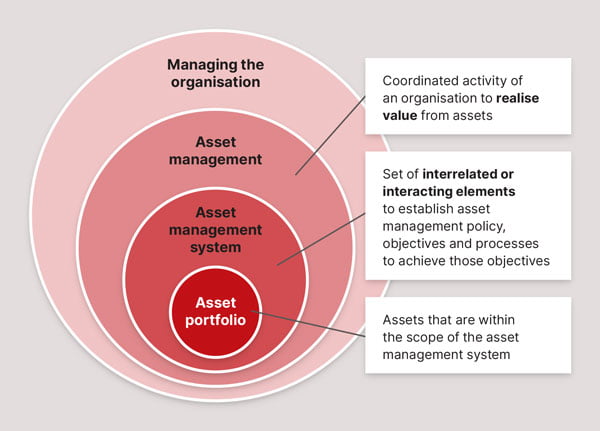
It’s unlikely that your organisation is best practice in all of the above – and equally unlikely that it is amongst the worst performers in every area. That means that you have room somewhere to improve your maintenance productivity and reduce your maintenance costs. To help you figure out where, watch out for our subsequent articles detailing each of the 5 keys in more detail.
Do you need a more effective preventive maintenance program?
We have over 21 years of experience in improving maintenance programs for a wide range of industries. Our services are catered to your specific business and operational goals, and we aim to be proactive in delivering solutions that are grounded in practicality and bottom-line results. Sound good to you?