There are a range of alternative approaches available for organisations and individuals to use when developing and optimising Preventive Maintenance programs. This article discusses some of these approaches, their strengths and weaknesses, and makes some suggestions regarding how you may select the best approach.
Each of the approaches we will discuss has a different level of rigour (and therefore time and cost) associated with it. These are illustrated in the diagram below. In addition, some of these techniques can be applied with a greater or lesser involvement of site operational personnel – the operators, maintainers and other stakeholders that are directly involved with the operation, maintenance and optimisation of the equipment.
Let’s discuss each of these approaches in a little more detail.
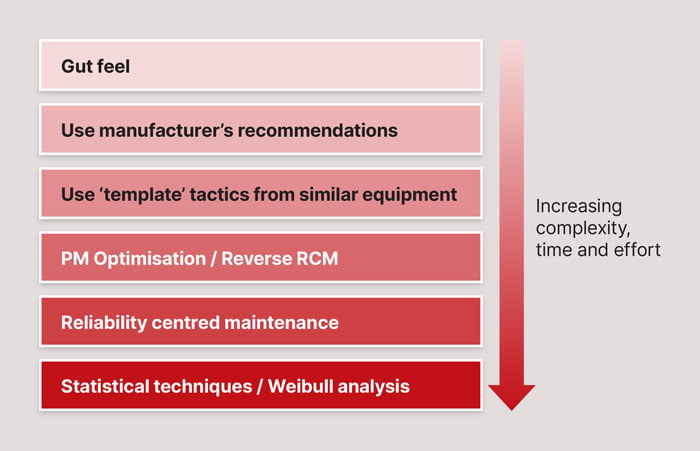
Gut feel
The quickest approach for developing Preventive Maintenance programs, this generally involves appointing an experienced “expert” to produce a PM program based solely on his or her experience.
The major advantage of this approach is its speed. PM programs can be generally put in place quite quickly. However care needs to be taken when adopting this approach as:
- You are totally dependent on the expertise and experience of the individual involved. Just because they have had experience in maintenance similar equipment previously does not necessarily mean that they understand the basis on which the preventive maintenance program for that equipment was developed.
- There are no guarantees that the four fundamental principles associated with sound PM program development will be applied
- The level of documentation associated with the development process is likely to be minimal, leaving no audit trail, and therefore ongoing optimisation of the program is more difficult and risky
Using manufacturers’ recommendations
The manufacturer’s recommended Preventive Maintenance program is a good place to start, when developing a PM program from scratch for new equipment. Indeed, if complying with the Manufacturer’s recommendations is a requirement in order to retain warranty on the equipment, you may choose to strictly apply these recommendations – at least until the equipment is out of its warranty period. Manufacturers generally have a fairly good idea of the common ways in which their equipment may fail, and it is wise to take advantage of this knowledge.
However, the manufacturer’s knowledge is incomplete in a number of important areas. Their recommended PM program is generic in nature. As a result, their recommended program generally does not take into account:
- The specific operating conditions under which the equipment will be operating in your environment, and therefore the likelihood of specific failure modes occurring on the equipment at your specific site
- The operating context of the equipment and the consequences of equipment failure at your specific site – and therefore whether or not the benefits of performing a specific maintenance task outweigh the costs or risks associated with not performing that task at your site
Manufacturers are keen to ensure that their equipment is seen as being reliable in the marketplace, so their PM programs tend to be based on “worst case” assumptions regarding the operating environment. In many cases, this leads to significant over-maintenance. The fact that manufacturer’s also generally sell the spare parts required in order to perform the recommended preventive maintenance also leads to a potential conflict of interest on the part of those manufacturer’s that you need to be wary of.
Using “template” preventive maintenance programs from other, similar equipment
In this instance, you use the PM tasks from another, similar equipment item that is used in a similar operating context as the starting point for PM program development. This approach is slightly better (in terms of quality of outcomes) than using the generic program recommended by the manufacturer.
However, there are still some potential limitations in this approach. In particular, “similar” does not necessarily mean “identical” – both in terms of the operating context and the specific configuration of the equipment. For this reason, this approach cannot be considered as being “plug and play”. Some work is still required in order to ensure that the PM tasks developed are appropriate for that specific equipment item in that specific operating context.
Preventive maintenance optimisation and reverse reliability centered maintenance
For the purposes of this article, we will assume that the PM Optimisation approach used is similar to a “Reverse RCM” approach. It is outside the scope of this article to describe what Reliability Centered Maintenance (RCM) or PM Optimisation (PMO) approaches are in detail, but there are numerous other articles on the web which describe this. A good summary of RCM is in the article The Seven Questions of Reliability Centered Maintenance while a similar summary of PM Optimisation/Reverse RCM can be found in the article Maintenance Analysis of the future.
The primary advantage in using a PM Optimisation approach is speed. If you have an existing PM program and reasonable failure history, then the list of likely failure modes for which PM tasks are to be developed can be derived quite quickly. In addition, a PM Optimisation approach fully applies all of the four fundamental principles associated with sound PM program development.
The risk with a PM Optimisation approach, however, is that it may be possible to overlook some failure modes using this approach. In particular, it may be possible to miss failure modes associated with Hidden Failures, or failures which occur infrequently. While there are some ways to minimise these risks in applying a PM Optimisation approach, if the equipment is highly critical, then this approach may not be rigorous enough.
Reliability centered maintenance (RCM)
RCM starts by defining all of the functions of an item of equipment, and then derives the Functional Failures and Failure Modes (failure causes) before progressing through a structured decision-making process to derive the optimum Preventive Maintenance task to apply to deal with each Failure Mode. The main weakness of this approach is that it is time-consuming (it may require up to 6 times more time and effort than a PM Optimisation approach) and may result in an extensive list of failure modes to be analysed for which Preventive Maintenance is either not technically possible, or cannot be justified. If RCM is performed correctly, however, it does result in a comprehensive list of the failure modes that may apply to a particular item of equipment in its current operating context. As with a PM Optimisation approach, it approach fully applies all of the four fundamental principles associated with sound PM program development.
Statistical techniques / Weibull analysis
Strictly speaking, this is not an approach for developing Preventive Maintenance programs, as these generally do not have decision making algorithms incorporated within them. However they can be effective when applied in conjunction with an appropriate decision-making approach (generally either RCM or PM Optimisation). If you have sound failure data, then analysing that data will definitely assist in making better decisions regarding your Preventive Maintenance program. However, in many cases, collecting, cleansing and analysing that data can be time-consuming. The typical issues that inhibit the effective use of statistical analysis techniques include:
- Failure to document all failure events in an appropriate computerised system
- Failure to accurately identify the causes of failure events (remember Core Concept number 2)
- Difficulties collecting data regarding suspensions
- Insufficient failure data (especially for very small populations of unique assets operating in specific operating conditions) to provide statistical accuracy
If the effort required to obtain and analyse meaningful data is significant, then careful consideration should be given to whether the benefits of utilising statistical analysis approaches outweigh the costs and effort involved. If the item of equipment is highly critical, or the preventive maintenance on that equipment is highly expensive or risky, and absolute accuracy in terms of the PM tasks selected is required as a result, then investing the time and effort in collecting accurate data and using these techniques may be essential.
Selecting the optimal approach
Clearly, it is only worth performing the more rigorous techniques where the cost and effort involved are outweighed by the benefits received. So how might you determine what level of rigour (and therefore what approach to take) is appropriate? One way is to first assess equipment criticality. This will help identify the most critical items of equipment – those items that represent the greatest business risks in terms of the consequences and likelihood of their failure. We discuss the assessment of equipment criticality in more detail in our article “Equipment Criticality Analysis – is it a complete waste of time?.”
Once the Criticality assessment has been completed, you could then develop a PM Review/Development strategy which ensures that the rigour applied is aligned with the level of criticality of each equipment item. This may look something like the table below (although the particular techniques chosen will clearly vary from industry to industry and organisation to organisation)
Criticality | PM review approach |
---|---|
Very High | Reliability Centered Maintenance (RCM) |
High, Moderate | Preventative Maintenance Optimisation (PMO) |
Low | Use manufacturer’s recommendations |
Negligible | Run to failure, or use manufacturer’s recommendations |
Note that you could apply different approaches not just to individual equipment items, but also to specific failure modes associated with those items. For example, there may be one failure mode on a particular item of equipment that, if it were to occur, could result in serious consequences. You may choose to analyse this with more rigour using a higher level technique. For example, you may choose to use statistical data to analyse that particular failure mode, if you have it. In some cases, the consequences may be so significant that you may even commission some reliability testing in order to collect the reliability data so that you make a better decision at some point in future.
As we have discussed in this article, there are a range of tools available for developing or optimising Preventive Maintenance programs. The key is to be practical, and keep a clear eye on the outcome that you are trying to achieve. Apply a level of rigour in analysis that is commensurate with the level of risk that you are trying to avoid, or benefit that you are trying to gain.
Do you need a more effective preventive maintenance program?
We have over 21 years of experience in improving maintenance programs for a wide range of industries. Our services are catered to your specific business and operational goals, and we aim to be proactive in delivering solutions that are grounded in practicality and bottom-line results. Sound good to you?