In the first article in this series on Maintenance Planning and Scheduling, we explored some of the “Big Picture” issues associated with the Planning and Scheduling process, people and capability to support the process, master data and KPIs.
In this second article in our series, we will dive a little deeper and explore in more depth, five of the common issues that affect the Scheduling process, namely:
1. Rework due to unplanned work being included in the schedule
The underlying premise of the maintenance Planning and Scheduling process is that by properly planning work before it is scheduled to the execution team, the work can be completed with optimum efficiency resulting in reduced equipment downtime and maximum productivity from the execution team, while minimising frustration for the execution team.
However, we often find this is not the case with unplanned work making it into the scheduling process and beyond. Some of the common symptoms we observe when this occurs, underlying causes and potential solutions are described below.
Symptoms
- Planner and/or supervisor chasing parts for scheduled work in the schedule week
- ‘Band-aid’ repairs as parts were not available to properly complete the work
- Work delayed due to need to chase up scaffolding, cranage etc
- Build up of backlog of work orders requiring further planning
- Poor KPI Compliance.
Common Causes
- No clear definition of what constitutes a properly planned job
- Work order status not used to distinguish ‘ready to schedule’ workorders from those requiring planning
- Lack of discipline around planning/scheduling process
- Supply chain dues-in reporting not working (parts that are ‘promised’ for the schedule are not on-site in time)
- Poor role definitions that don’t adequately outline responsibilities
- Proliferation of break-in or break
Solutions
- Clearly define parameters for a properly planned job – work steps, parts, specialist equipment, services/contractors, permitting, etc.
- Establish a clear policy regarding only planned work being permitted into the schedule
- Establish guidelines for assumptions in relation to part availability (is a job ready to schedule when parts ‘should be on site’ in time, or when parts have physically arrived?)
- Make use of work order status codes to distinguish whether a work order is ready to schedule, including rules around who can change status and on what basis.
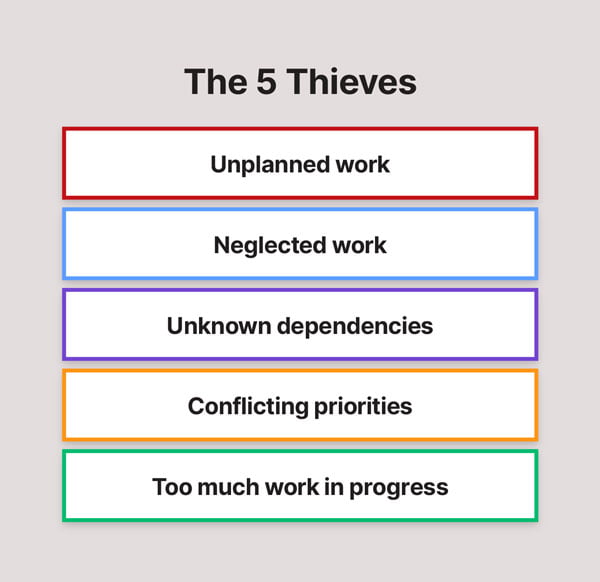
2. Capacity Management
The role of the maintenance scheduler is to understand the work that needs to be performed, the priority of that work, the availability of the equipment to be worked on, and the capacity of the maintenance team to perform this work and to then load the schedule accordingly.
Typically, we see businesses scheduling enough work to occupy 80-85% of crew capacity. This provides some capacity to deal with breakdowns etc. Of course, this target varies depending on how the maintenance teams are structured. A site with a dedicated PM crew and a separate breakdown crew might schedule the PM crew to 100%, and the breakdown crew to perhaps 30% of capacity.
Of course, the underlying assumption is that the scheduler understands what actual capacity will be available, and this will be influenced by a range of factors, annual leave, contractor availability, overtime availability etc. And more often than not, keeping this information up to date is up to someone else in the organisation – HR, the supervisor, etc.
Some of the common symptoms we observe when this process isn’t working, underlying causes and potential solutions are described below.
Symptoms
- Schedule compliance seems to be erratic
- A large number of unproductive hours are allowed for when capacity planning (schedule loading is consistently low)
- Schedule compliance consistently low
- No value seen in rough cut capacity planning
- Forward log piled up a few weeks ahead of schedule week
- Poor KPI Compliance – Capacity Utilisation.
Possible Causes
- Schedule loaded to a consistent high level based on maximum work centre capacity resulting in erratic schedule compliance (OK when team is all there, instant fail when team is below strength)
- Schedule loaded conservatively (absences allowed for even though they may not eventuate)
- Lack of clarity around forward capacity means forward planning is seen as a waste of time
- One schedule loading target used irrespective of work-centre objectives (i.e. using a target of 85% for both the PM crew and the breakdown crew)
- Labour estimates for planned work are inaccurate resulting in under/overloading of schedule in actual terms
Solutions
- Develop a capacity model with Management signoff on agreed percentage.
- Clearly define in above agreement what (if any) proportion of labour will be excluded from capacity to cater for unplanned events.
- Establish processes to ensure forecast capacity (i.e. considering know leave absences) is loaded into the system and kept up to date
- Establish appropriate KPI’s to monitor problem areas … planned hour versus actual hours if the accuracy of planned hour is a challenge; monitoring schedule loading and schedule compliance to understand correlation between the two, etc.
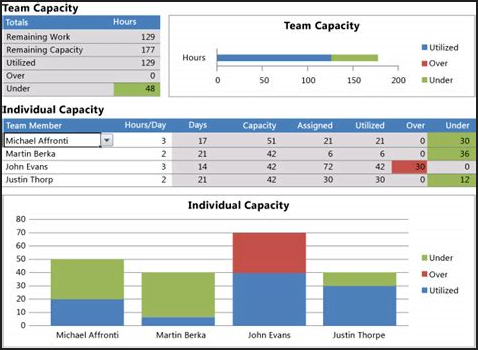
3. Setting priority on work
As noted in the previous section, understanding the priority of work is critical to establishing an effective maintenance schedule. The use of an agreed work order priority system gives the Planner/Scheduler the ability to categorise work quickly and ensure high priority tasks are given greater consideration when building a weekly execution schedule. It also helps the supervisor make informed decisions about which work orders can be deferred if break-in or breakdown work needs to performed.
Some of the common symptoms we observe when this process isn’t working, underlying causes and potential solutions are described below.
Symptoms
- Work orders in the CMMS have no priority coding
- Work orders are frequently reprioritised during the scheduling meeting based on a key individual’s personal preferences
- Moving high priority work out of schedule when an unplanned event occurs.
- Low priority work keeps being rescheduled without a priority review.
Possible Causes
- Work Order priority not set up in CMMS
- No agreed rules for assigning work order priority including definitions and decision right (who has ultimate say on what the priority is)
- No agreed rule for loading the schedule (if everything is a priority, then nothing is a priority)
- No priority review process to address low priority work that has been rescheduled several times
Solutions
- Establish a set of work order priorities, the definitions associated with each priority, and decision rights including around who has the final say on priority
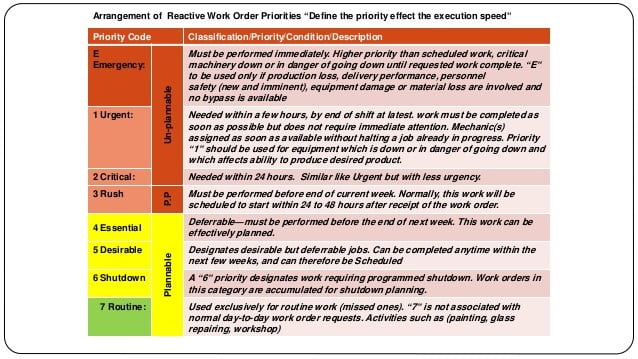
- Develop a priority review process with Execution group. Establish clear intent and responsibilities. Would suggest this is added to daily notification meeting with Supervisor.
- Agree on a set percentage to include all work priorities for a scheduling period to help with having to move work to accommodate unforeseen events. i.e.
- 80% High priority jobs
- 10% Medium priority jobs
- 5% Low priority jobs
- 5% Very low priority jobs
4. Scheduler has become a slave to the system
Scheduling maintenance work is without doubt once of the most complex interactions that uses have with their business systems. It requires understanding what work is needed, when equipment will be available, who can work on the equipment, and then assigning the work for execution. In the past, work was often scheduled as a weekly block to a work crew with the supervisor left to figure out who was best placed to perform the work and when. Increasingly these days, businesses are attempting to schedule ‘to the individual/to the day’, and sometimes to this level of accuracy two weeks ahead of the schedule window.
The process of scheduling can sometimes be so labour intensive it defeats the purpose of its intent.
This is particularly true when scheduling to the person to the hour in a day which frequently leads to:
- The Scheduler focussing solely of producing the correct system outcome, irrespective of its ability to be executed in reality
- Unrealistic schedules which are at best used only as guidance and at worst ignored – particularly where the planning accuracy is poor, or the scheduler does not fully understand the capability of the execution team
- Supervisor’s spending excessive time rescheduling work
- Increases frustration and compromise of safety standards
- Intentional shortcutting of process
We always recommend walking before running and find that scheduling to the crew to the day for the week ahead, and allowing the supervisor to assign work to the team is a solid starting point. Going beyond this usually requires more sophisticated scheduling tools than those provided by the typical CMMS, and if the underlying data such as actual resource availability or work order planning accuracy isn’t right, then these can represent a lot more work with no tangible benefit.
5. KPI’s driving wrong behaviour
We have already covered KPI’s and their positive/negative effects in Planning and Scheduling in Part 1 of these articles.
The scheduler is often seen as the focal point for schedule related KPIs such as schedule loading and schedule compliance. In reality, they have only part responsibility for each.
Schedule loading is the amount of work scheduled as percentage of available crew capacity – the scheduler has no control over available crew capacity.
Similarly, schedule compliance is the amount of scheduled work that was complete, as a percentage of the amount of work that was scheduled. In this case, the scheduler has no control over the amount of work complete.
If management chose to use the KPIs as an indicator of overall process performance, then these measures are appropriate. But if management uses these measures for performance management, then we typically see the following behavioural changes to meet a target:
- Scheduler will over/under load schedule hours as discussed in capacity management section.
- Execution will find ways not to execute work and blame poor planning/scheduling as reason.
- Trust issues will arise between work groups due to blame culture.
I hope that this article has given you some useful tips for better understanding “Scheduling Pitfalls” aspects of Maintenance Planning and Scheduling. Understanding the pitfalls can make your job as a Scheduler more productive and satisfying, help your organisation to reduce costs and be more effective.
To get more information on how best to develop and embed a robust work management process please read Part 1 of this article series for hints and tips. If we can help you be more effective as a Scheduler, contact us. Or you may want to consider attending our Maintenance Planning and Scheduling Excellence training course where we give you even more practical tips on how to be a more effective Maintenance Planner and/or Scheduler.
-
Product on saleMaintenance Planning and Scheduling Excellence$1,935.00 – $2,150.00
-
Product on saleIntroduction to Maintenance ManagementOriginal price was: $1,075.00.$967.50Current price is: $967.50.