In the first in this series of articles, we mentioned that any improvement process is headed for failure without the buy-in and support of all those involved; it is imperative that the leadership and culture is focussed on being proactive rather than reactive, and is performance driven. In addition, we stated that the development and implementation of a ‘balanced scorecard’ of Key Performance Indicators (KPIs) and the support and communication from management are the keys to delivering improvement. In this article we will expand on these thoughts.
This is the fifth in a series of six articles on improving Maintenance Productivity through the use of Lean Maintenance techniques.
Creating a proactive and performance-driven culture
What is culture? A simple definition is “the way we do things around here”. If you want a more complex definition that, in essence, means the same thing, you can define it as “The values and behaviours that contribute to the unique social and psychological environment of an organization” (see BusinessDictionary.com).
Let’s consider Ledet’s model of Operational Improvement, illustrated below.
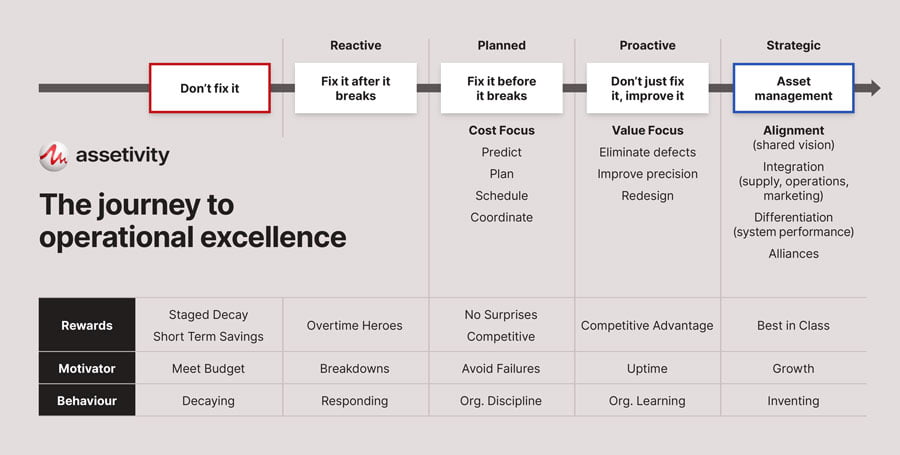
An explanation of this model in its totality is beyond the scope of this article, but let’s briefly outline the key elements. Ledet and his associates proposed that, based on their experience in improving operational performance at Dupont Chemicals and Specialities in the 1990s, that individual work sites tended to operate in one of five “domains” – those entitled, “Don’t Fix It”, “Reactive”, “Planned” etc. in the above diagram. Further, in the context of this article, they noted that the underlying behaviours and culture at each site differed, depending on which domain the site was operating in. Clearly, organisations want to move to the right in this diagram – the aim, as a minimum is to move into the “Proactive” domain.
The key elements of organisational culture in this domain are:
- A focus on maximising value to the organisation, not just on reducing costs.
- Motivation driven by a desire to maximise equipment uptime, rather than just avoiding failures
- Behaviours that are supported by “learning” culture – a focus on identifying newer, better ways of doing things, rather than a “compliance” culture (as tends to be the focus in the Planned domain), or a “responding” culture (as tends to be the main focus in the Reactive domain)
Clearly, for Maintenance technicians to be productive, their work needs to be properly planned and scheduled, and their needs to be a high level of commitment and discipline in adhering to the plan wherever possible (as we discussed in Part 3 of this series), and so, in this sense, there needs to be a high level of compliance. But productivity improvement also requires a focus on eliminating the causes of failure (as we discussed in Part 4 of this series), and this requires a learning culture. One of the challenges that leaders face is how to get the balance right between enforcing compliance (continuing to do what we currently do, with a high level of discipline), and encouraging improvement (challenging what we currently do, seeking a better way). One of the key management tools that can be used to drive the right behaviours is the appropriate use of performance measures. We will discuss this later in this article.
Leadership as a driver of organisational culture
So how do you go about establishing a better culture (assuming that you need to realign the culture to make sure that productivity really is a priority, and that people do the things they are supposed to do to assure maintenance productivity)? Changing organisational culture is notoriously difficult and takes considerable time. And one of the truisms is that focused culture change can only happen when it is driven from the top down. Leadership is essential. However, let’s make it clear that this does not mean that meaningful culture change requires the CEO to drive it. Leadership is independent of organisational position, and if you are a Maintenance Manager, or a Maintenance Supervisor, or even a Reliability Engineer, you can still shape the culture within your circle of influence. For example, the behaviours of your work team can be shaped to align with the type of culture that you wish to exist. However, there will be limits to what you can achieve at lower levels in the organisation – particularly where your people interact with those from other workgroups who may not share the same cultural beliefs. Nevertheless, you CAN make a difference.
One of the most useful (and visual) models that I have seen which describes the various tools that can be used by leaders for changing organisational culture is one outlined in an article by Steve Denning (read How Do You Change An Organizational Culture?) in Forbes magazine. This diagram is reproduced below.

I find this diagram useful in drawing the distinction between Leadership Tools (the “softer” stuff), Management Tools (which we engineers typically focus on most) and Power Tools (which we sometimes resort to, but should be avoided if possible). Using the Power Tools for culture change can lead to short-term grudging compliance, but any behavioural changes will not be sustained (“the floggings will continue until morale improves”).
Denning points out in his article that effective culture change requires the right balance between the use of Leadership Tools (creating an inspiring vision and continually communicating it, finding and telling stories that inspire alignment with the new vision, walking the talk etc) and Management Tools (ensuring that roles and responsibilities are clear, establishing the right performance measures, recruiting the right people, ensuring that the organisation has the right competencies etc). In my experience in most maintenance organisations, maintenance leaders (Managers, Superintendents, Supervisors, Engineers) are more comfortable using the Management Tools than the Leadership Tools. However those that swing the balance to increase their use of Leadership Tools frequently achieve great results – these are the ones that you see collecting the awards for outstanding Maintenance performance.
There is insufficient space in this article to do full justice to the topic of Leadership (perhaps a future article), but please do note that Leadership is one of the 5 pillars in the SMRP Body of Knowledge, as well as being prominent in most other models of Maintenance, Reliability and Asset Management improvement. It is also a key compliance area (one of seven) in the ISO standard for Asset Management, ISO 55001. So I encourage you to read more on this topic, and consider whether you are actively applying Leadership tools often enough and well enough in your current role.
Using performance measures to change behaviour
One of the most powerful management tools that can be applied to change behaviour is the appropriate use of performance measures, when combined with an effective performance management process and reward system.
You can read a more detailed article on the use of Performance Measures here, but in the context of Maintenance Productivity, there are three tips that are essential for success:
- The measures that you select are absolutely critical, and need to be chosen to drive the behaviours that you are seeking. If you are seeking compliance with procedures, then you will need to establish some form of measure that determines whether this is occurring. If you are seeking to eliminate the causes of failures, then once again, you will need to establish some form of measure that determines whether this is occurring. Measuring an output, without some form of measure that indicates whether the desired behaviours were applied in achieving that output is generally too indirect. However, do not lose sight of the fact that the desired behaviours are intended to produce a desired outcome (so somewhere you will need to measure the outputs). If you and your people are doing the right things, but not achieving the right results, then you will need to reconsider the direction you are heading.
- Too few measures is better than too many. Give someone twelve measures against which their performance is being evaluated, and all that happens is that you confuse them. They will probably focus on the 3 or 4 that means most to them (and which are the easiest for them to achieve target performance on). Far better for you (as a leader) to pick the 3 or 4 that are most important to the organisation, and ensure that they buy into those measures and align their behaviours with the achievement of those measures.
- Measurement without subsequent action is simply a waste of time and money. As a leader, you MUST ensure that effective actions are generated any time that performance does not meet target. Similarly, you MUST ensure that rewards (not necessarily financial) are given when performance expectations are met or exceeded.
- There is no point in holding someone accountable for performance which they cannot influence. You will almost certainly need to establish different measures for different work groups, and possibly for different individuals within those workgroups.
Conclusion
In this article we have outlined how culture, leadership and performance measures can reinforce and drive a focus on Maintenance productivity improvement. In the next (and final) article in this series, we will discuss the bigger picture.
Do you need a more effective preventive maintenance program?
We have over 21 years of experience in improving maintenance programs for a wide range of industries. Our services are catered to your specific business and operational goals, and we aim to be proactive in delivering solutions that are grounded in practicality and bottom-line results. Sound good to you?