In previous articles we have discussed what good Maintenance Planning and Scheduling looks like, offered five tips for more effective Maintenance Planning and Scheduling, and discussed the Do’s and Don’ts of Effective Maintenance Planning.
However, regardless of how good (or bad!) your Maintenance Planning and Scheduling processes are, if you want to make them more efficient and effective, you will need to implement an effective process for continuously improving them.
What is continuous improvement?
‘Continuous improvement’ often causes people to think ‘Improvement Project’, but the two are not the same.
While a ‘project’ has a defined beginning and endpoint, a continuous improvement process never ends. It evolves, it breathes and it is alive. It is part of the everyday routine of “business as usual”. And as is the case with all routine processes, it requires an ongoing investment of time and energy in order to be sustained.
At the heart of all continuous improvement processes is Deming’s Plan-Do-Check-Act cycle.
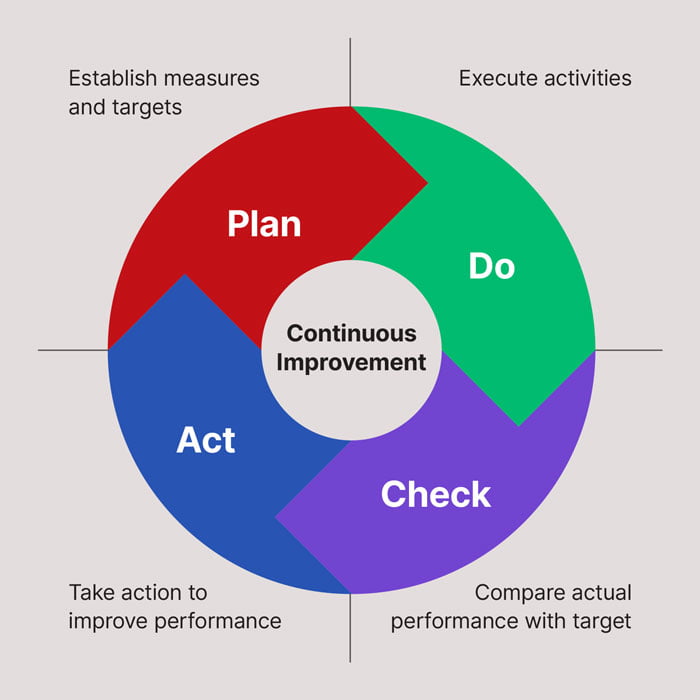
The key steps in this cycle are:
- Plan – determine the critical success factors for the process you are trying to improve, establish measurements that will assess your performance in these key result areas, and establish targets against which actual performance will be compared.
- Do – execute the process which you are measuring and capture the data which allows you to assess the performance of that process
- Check – compare actual performance with the target previously established and understand the reasons for variances
- Act – implement the actions necessary to make improvements
So how does this apply to Maintenance Planning and Scheduling?
The maintenance planning and scheduling process
The Maintenance Planning and Scheduling process, in simplified form, can be considered to consist of 5 major steps, as illustrated below:
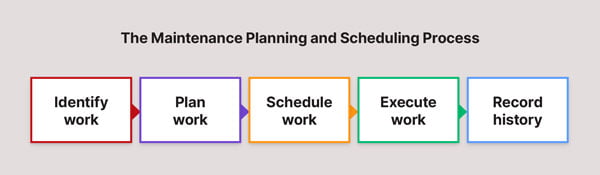
The above process includes activities for Plan and Do, but has no feedback loop for Check and Act.
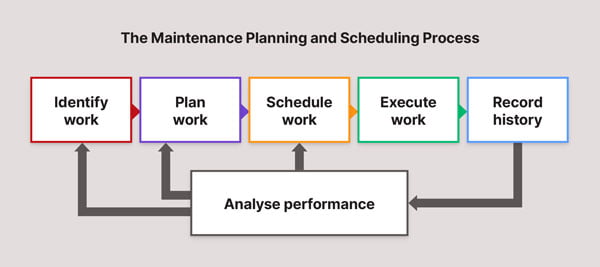
Let’s examine each of the three feedback loops in turn, and for each of these consider:
- Why they are important
- What performance measures you might consider in this loop
- How you might set performance targets for these performance measures
- How and how often you might assess performance
- Typical improvement actions that may arise
Are you doing the right work?
The first performance loop we will examine is:
Record History -> Analyse Performance -> Identify Work
The primary objective of this feedback loop is to determine whether you are doing the right maintenance work. This could include an assessment of:
- Whether the Preventive Maintenance program is preventing failures effectively
- Whether the Preventive Maintenance program may be able to prevent failures more efficiently
- Whether defects and incipient failures identified from Predictive Maintenance inspections or other sources are being completed in sufficient time to avoid in-service failures
As such, the primary objective of this feedback loop is to improve plant and equipment reliability. As a result, the key measures that may be considered as part of this feedback loop include:
- Plant and Equipment Reliability (MTBF)
- Number of breakdown or unplanned work orders completed
- Unplanned Plant Downtime
Of these, the second and third are probably the easiest to implement, and targets for these should be set which represent an improvement on past historical performance.
We recommend that, on a weekly basis (or fortnightly, depending on your planning cycle), the maintenance leadership team should review performance in this area at a regular meeting, and ensure that significant unplanned work orders or events are investigated. This may also occur at a routine daily review of the previous day’s performance.
The key to making improvements in this area is to ensure that the root causes of these unplanned events are identified, and permanent solutions implemented which address these root causes. This is beyond the scope of this article, but you may be interested in reading our article “Defect Elimination: Was the problem really solved?[SD4] ”. In terms of the Maintenance Planning and Scheduling process, the most likely potential improvements actions that may arise from this investigation include:
- Making revisions to Preventive/Predictive Maintenance Strategies
- Improving the quality/content of Maintenance Work Instructions
- Changes to the prioritisation process for Work Orders to ensure that defects requiring urgent attention are actioned prior to equipment failure
Are you planning maintenance work effectively?
The second performance loop we will examine is:
Record History -> Analyse Performance -> Plan Work
The primary objective of this feedback loop is to determine whether maintenance work is being effectively planned. At this point it is worth emphasising the difference between Planning and Scheduling.
- Planning is determining what you need to do and what resources will be needed in order to perform a given Maintenance Work Order.
- Scheduling is determining when the Work Order will be performed, after considering when the required resources (including the equipment to be worked on) will be available, and the priority of this work in comparison with competing alternatives.
Ensuring that work is effectively planned is important because:
- Well planned work can be performed in a more controlled and safer manner
- Well planned work can be performed more efficiently, and improves maintenance tradesman productivity
- If important resources are omitted from the plan (such as spare parts required), then there is a risk that these resources may not be available at the time the job is scheduled to be performed – leading to the potential for rework or poor quality work, with a resulting adverse impact on equipment availability and/or reliability
The key question to consider here is who is in the best position to determine whether a Maintenance Work Order was effectively planned. In our view, the person that is best able to make that judgement is the maintenance tradesman or technician who performed the work. Questions that they should be asking include:
- Did the Isolation procedures, Safety instructions and/or Hazard Assessments on the work order comply with company and/or legislative standards and were they adequate?
- Were all the resources needed to perform the work (parts, tools, labour, special equipment etc.) accurately identified on the Work Order
- Was the time allowed to perform the job (both duration and labour hours) sufficiently accurate?
- Were the work instructions complete, clear, easy to follow and in the correct sequence?
If there are issues in any of these areas, then it should be the responsibility of the person performing the work order to note suggested amendments on the work order prior to it being closed out. If paper work orders are being used, then these paper copies should be returned to the Maintenance Planner for action. If a paperless system is in place, then the Maintenance Planner should receive electronic notification of the need for amendments.
There are several ways that performance data relating to Maintenance Planning Quality can be captured within a Computerised Maintenance Management System. This could include:
- Using a work order completion code to indicate that amendments to the job plan are required
- Reporting all work orders where actual labour hours required vary significantly from planned labour hours
- Raising a separate work request or notification (assigned to the Planning work group) for each job plan requiring amendment
Whatever performance measure is used, this should be reported on weekly (or fortnightly, depending on your planning cycle), and reviewed by the maintenance leadership team.
In addition, the leadership team should proactively manage the number of outstanding amendments required. There is little point in having maintenance technicians provide feedback on the quality of job plans if no action is taken based on this feedback. One organisation that we work with has set itself a target of having all technician feedback actioned within 48 hours of it being received by the planning group. Having a target such as this provides a solid incentive for continuous improvement – but only if performance against this target is measured and acted on.
Are you scheduling maintenance for the right time?
The final performance loop we will examine is:
Record History -> Analyse Performance -> Schedule Work
The primary objective of this feedback loop is to determine whether maintenance work is being effectively scheduled, and whether work is actually being performed at the scheduled time. As mentioned earlier, Scheduling is about determining when a specific job should be done.
Whether work is performed at the scheduled time may or may not be important.
Under certain circumstances, performing work at the scheduled time may be very important. For example:
- When equipment has been shut down specifically so that the maintenance can be performed at that time
- When external resources have been brought in (at additional expense) to perform the work at the scheduled time
- When the work can be performed more efficiently if it is done at the scheduled time
- When other work can be performed more efficiently if this work order is done at its scheduled time
In particular, work performed during planned plant shutdowns tends to be highly time-critical. It is vitally important that this work is done at the scheduled time, otherwise the knock-on effect for other work and the entire shutdown may be significant.
In other situations, it may be less important exactly when the work is performed, but still highly important that it is done prior to a “required by date”. For example, it may not be important exactly which day a safety inspection on a crane is performed, but vitally important that this task is completed within 12 months of the previous inspection, otherwise statutory requirements may not be met.
It is important that the measures you use for assessing and improving scheduling performance take these differences into account – or at the very least, when interpreting the results, an eye is kept on the ultimate objective – to ensure that the right maintenance is done efficiently and effectively.
With this in mind, some of the performance measures that can be used in this feedback loop include:
- No of Preventive Maintenance tasks passed their “required by” date
- No of Corrective Maintenance tasks passed their “required by” date (which implies that you have a solid process for determining what this “required by” date should be)
- Schedule Compliance (the % of Scheduled Work completed during the review period)
Of these measures, Schedule Compliance is frequently the most misused (and even abused) measures. Why this is so could be the subject of an article in its own right, but in our experience, an over-emphasis on achieving high levels of Schedule Compliance can frequently be counter-productive. It frequently drives behaviours that include:
- Doing only Scheduled Work, even though operating circumstances change and doing other work would actually drive better business outcomes (such as performing Opportunity maintenance during an unplanned plant shutdown)
- Doing Scheduled Work, even though that work has not been well planned, and as a result takes considerably longer than if it had been deferred awaiting proper planning
- Doing Scheduled Work, even though all the resources required to perform that work are not available (e.g. spare parts), and it would have been better to defer the work until all the parts were available, rather than do a part-job and have to perform rework later.
Nevertheless, as a general rule, we should aim to complete work as scheduled – and to ensure that the work is adequately planned and scheduled to allow this to happen.
Once again, we recommend that, on a weekly basis (or fortnightly, depending on your planning cycle), the maintenance leadership team should review performance in this area at a regular meeting, and ensure that significant variances from target are investigated, the underlying root causes identified, and appropriate actions taken to address these. Note that the opportunities for improvement may lie in the area of improving the quality with which maintenance is scheduled (e.g. schedulers should do a better job of making sure that all resources will be available at the scheduled time for the job), or with the execution team (e.g. just because you don’t want to do that job at that particular time is not a valid reason for not doing it at that time).
Five tips for more successful planning and scheduling improvement
Here are five tips that we think will help you embed continuous improvement as part of your Maintenance Planning and Scheduling Culture.
1. Always review the previous week’s performance
As part of your routine weekly (or fortnightly) planning schedule, make sure to include a review of the previous week’s planning performance as an agenda item at one of your planning meetings. These meetings should ideally be attended by representatives from Maintenance Planning, Maintenance Execution, Production/Operations and be chaired by a senior Operations or Maintenance role. This review must happen as a matter of routine, and must also effectively identify the underlying root causes of failure to meet target and initiate actions to address these causes.
2. Track completion of the improvement actions
Following on from the previous item, the improvement actions identified must be completed, and the status of all outstanding actions must be monitored and reported against. Whether this is done using a Lean Board approach or some other method, those assigned actions which they have to complete must be held accountable for getting them done in a timely manner. Reviewing the status of these at the weekly Maintenance Planning meeting is a good way of making sure they don’t get forgotten.
3. Choose performance measures wisely
Good performance measures are vital to continuous improvement. As we have discussed earlier, some performance measures, if incorrectly used, can drive inappropriate behaviours. But good performance measures give you an ability to see gaps in past performance and behaviour so that you can improve these in future. We have suggested some performance measures for continuous improvement in Maintenance Planning and Scheduling earlier in this article – but it is more important that you choose measures that you believe are most appropriate for your organisation and that will drive the improvement behaviours that you are seeking.
4. Get the data right
Having good performance measures is of little value if the data that is used to calculate them is incomplete or inaccurate. It will be important to make sure that there is an appropriate level of rigour applied in making sure that accurate and complete data is recorded, and any quality issues addressed as quickly as possible. As most of the data used for assessing Maintenance Planning and Scheduling performance is generated from work orders, there is frequently a need to remind your maintenance technicians, supervisors and planners of the need to:
- ensure that work orders are closed out promptly after completion of the work, and
- ensure that all required codes are accurately completed – in particular codes that indicate whether work orders were planned or unplanned, scheduled or unscheduled
Bear in mind that the more you engage, review and use your data the more motivated people will be to make sure it is accurate and to improve it. All data will be imperfect, but this shouldn’t stop you from starting to use it – as using it will force you to improve it.
The flipside to this is if you are not using and improving your data then do yourself a favour, stop recording it. Your team will know if the data they are recording is used, and it will affect the quality and consistency of what they record. When a maintainer writes feedback on a task they will see if their feedback was used the next time they do it. If the task is unchanged they are less likely to give feedback again. It may only take this one experience for a maintainer to give up altogether. If no one is monitoring data quality you may lose months of valuable data.
5. Be aware of the “grieving” process
When you first start to implement a continuous improvement process for Maintenance Planning and Scheduling you can expect people to go through a similar process to when they experience extreme grief. The key stages in this process are as follows:
- Denial– “I have seen all this before. Management fads come and go. If I ignore it eventually it will die a natural death and we can go back to the good old days where we could just do what we wanted.”
- Anger – “The data must be wrong. The measures can’t be being calculated properly. This can’t really be my performance – these performance measures are crap.”
- Bargaining – “If you want me to improve performance in this area, what do you want me NOT to do while I am working on this”
- Depression – “Let me work on my CV. There has to be a better place to work than this”
- Acceptance – “Ok. I can see the need to improve. I guess I will just have to knuckle down and do what I can to make those improvements.
Persistence and empathy is required to get people through to acceptance and to embed continuous improvement in Maintenance Planning and Scheduling as part of the normal way things are done.
Conclusion
Continuous improvement should be an ongoing part of your organisational culture that never ends. If you haven’t already embedded this within your Maintenance Planning and Scheduling process, then start now. Book a review meeting with your team, pull out your current data, even if it’s questionable, and start using it! Do it this week!
We can help you to establish performance measures and continuous improvement processes that drive ongoing performance improvement. Please contact us to discuss your needs and we will do our best to assist.