Introduction
As part of the operational readiness process for new plant, a Reliability Block Diagram (RBD) model can be used during the design and commissioning phases to assess system reliability and ensure production targets can be met consistently. Mining operations depend on the seamless integration of complex systems—such as crushers, conveyors, mills, pumps, and control systems—where the failure of a single component can halt production. An RBD helps identify how component failures impact overall plant reliability and availability.
RBDs are particularly useful when analysing systems that include critical equipment arranged in series (where each must function for the system to operate) or include redundancy (such as backup pumps or parallel crushing streams). By modelling these relationships, RBDs allow plant engineers and reliability specialists to estimate system availability and identify weak points before operations begin.
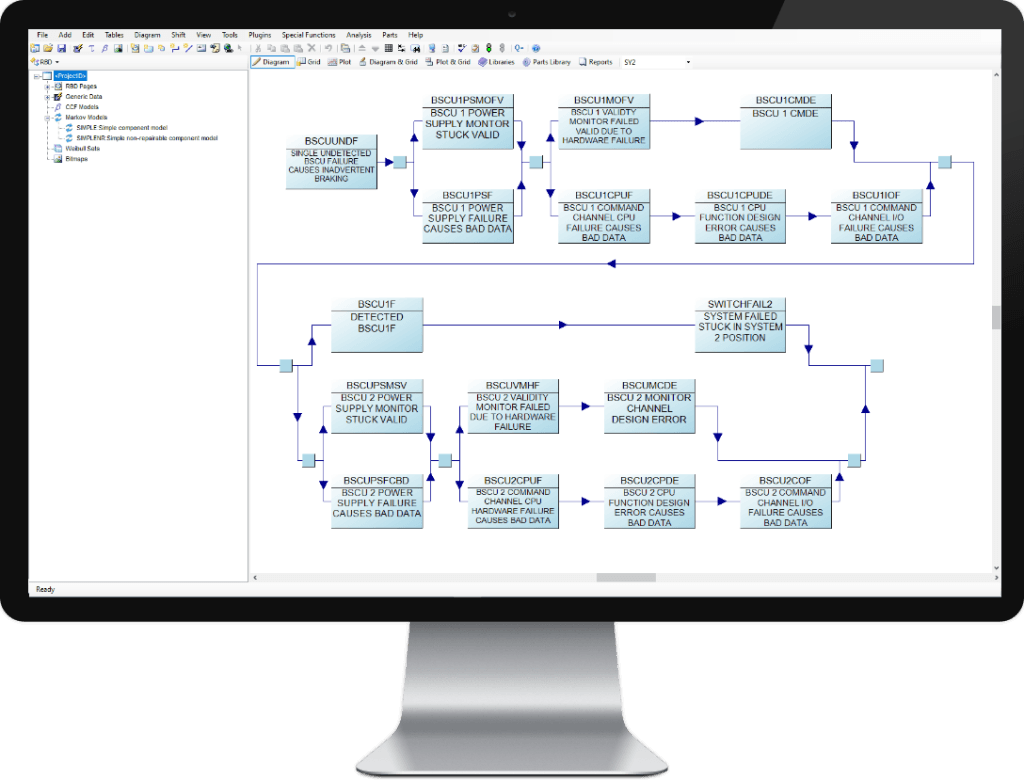
Reliability Block Models during the Design Phase
During the design phase, RBDs can be used to test different configurations—such as adding redundant crushers or backup pumps—to understand their impact on system uptime. These simulations inform risk assessments and help justify investments in redundancy or automation, improving long-term productivity and reducing unplanned downtime.
RBDs can also be used when selecting equipment, as these can help to specify the reliability and availability required from equipment if production targets are to be met, and alternative equipment options can be assessed in the light of these specifications.
RBDs also help to determine optimum spare parts inventory levels, develop optimum preventive maintenance strategies, and quantify the resources required to support effective operations.
Reliability Block Models during the Commissioning Phase
During the commissioning phase, the reliability specifications in the RBD can be used as a baseline against which equipment can be tested. If equipment does not meet the expected reliability requirements, action can be taken to address this sooner, rather than later, therefore contributing to faster ramp up to full production.
Moreover, RBD models contribute to compliance and risk documentation required for operational readiness reviews. They provide a clear, visual representation of the plant’s reliability structure, making it easier to communicate risks and mitigation strategies to stakeholders.
Conclusion
In summary, using a reliability block model as part of operational readiness for a new plant enhances system design, can be used to validate the performance of new plant, facilitates the development of optimum preventive maintenance strategies and spare parts holdings, and ensures the plant is equipped to meet performance goals from day one. It’s a proactive tool that bridges engineering design with operational reality.
Assetivity has the capability to develop Reliability Block Models. If you are interested in learning more, please do not hesitate to contact us.