“The best years of your life are the ones in which you decide your problems are your own. You do not blame them on your mother, the ecology, or the president. You realize that you control your own destiny.”
Albert Ellis
How many times have you come across an issue in your workplace where:
- You came across a damaged piece of equipment?
- You discovered some spillage?
- You found someone working unsafely?
- You just uncovered something ‘wrong’?
Being the diligent professional that you are, you contained the problem, you informed the area supervisor of the problem, and you witnessed the immediate corrective actions to rectify the problem.
All fixed, right?
“Problems are to the mind what exercise is to the muscles, they toughen and make strong.”
Norman Vincent Peale
Well, that depends on your idea of the problem and your definition of solved.
Yes, the issue was a problem and, yes, the issue got ‘cleaned up’, which is the proper initial action. However, the true problem in all probability still remains.
The true problem is that the response was only reactive and failed to include any real corrective or preventive actions. We think that simply rectifying the issue quickly and moving on is all that is needed. In effect, the ‘real’ problem identified remains hidden.
- We did not carry out any form of RCA / five whys.
- We did not look for other similar / damaged conditions.
- We did not change a single process.
- We did not stop the issue from occurring again
- We did not change the culture of acceptance
- There was no Kaizen / Continuous Improvement action or plan,
Basically we just put a big Band-Aid over the problem without actually removing the root cause, or even really changing anything; so we are doomed to repeat this cycle another day, over and over again.
We as maintenance and reliability professionals pride ourselves in conducting thorough analyses of physical equipment issues, planning PM and PdM strategies to cover the failure modes and maybe even implementing a CI process, but how often do we make that level of commitment to the non physical maintenance aspects of our business?
“Every problem has a gift for you in its hands.”
Richard Bach
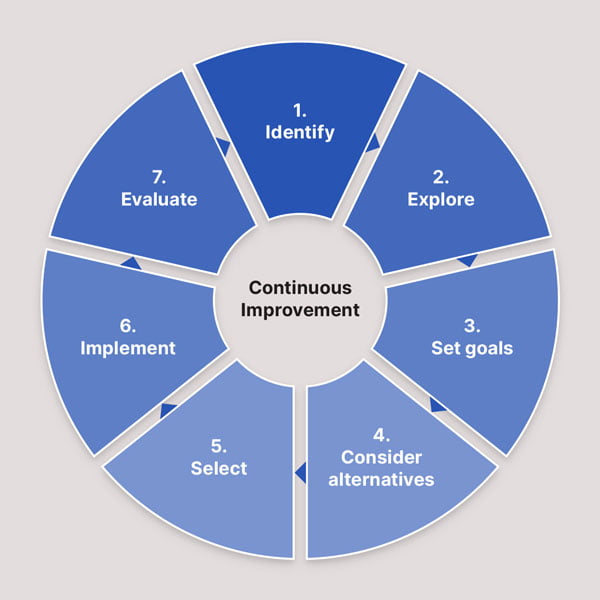
So next time you uncover an issue, what are you going to do differently? Are you doomed to repeat the same cycle?
If you enjoyed this article and want to receive notifications of future articles that we publish, please sign up for our newsletter here.