Most organisations have some sort of investigation process, ranging from a basic incident report form through to a mature Root Cause Analysis (RCA) process. Organisations have recognised the importance of learning from past failures and events.
How many of these organisations would consider their RCA process to be achieving its full potential? We suspect not many!
Why do these processes often fail to meet expectations and reach their potential? We have had the privilege of working with many organisations over many years giving us insights into the common themes that prevent RCA process from working to their full potential. These insights have allowed us to develop the following 5 Tips to help you get the most from your RCA investigations.
Tip 1: Develop a repeatable process, not a perfect one.
Once an organisation recognises the need for an RCA process they usually invest in some RCA style training. Once a core group of potential investigators have been trained it would be reasonable to expect that some good outcomes are just around the corner! However while you may get some early wins, you will find that they are not sustainable without a repeatable and sustainable process.
You don’t need a perfect process, there is no such thing! Instead focus on making your process simple repeatable and sustainable. Ask yourself the following questions:
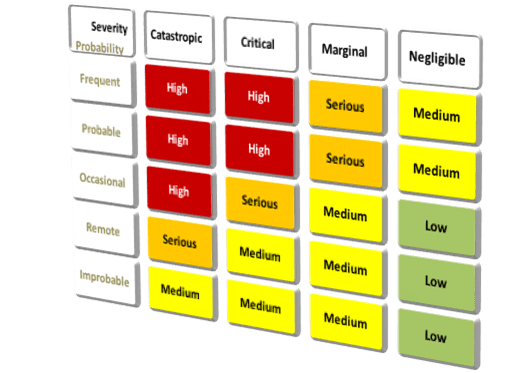
What triggers an RCA investigation in our business?
No organisation has the resources to run an investigation on every single failure, event or incident. There needs to be a way of selecting the ones that will deliver the greatest benefit. A basic risk matrix tool, aligned to your business, can assist in ensuring that you are investigating the failures or events that will deliver the greatest benefit. Be aware that a risk assessment tool can be used to confirm you pre-existing views and biases.
Be honest with yourself and allow it to drive your thinking, not the other way around.
Are we reactive or proactive in the triggering of our investigations?
Do you wait until a reoccurring fault has caused significant delays, costs or losses before an RCA investigation is started? Does the boss have to tell us which events to investigate? Use data to predict future trends and then run RCA investigations to avoid them. Don’t wait until the reoccurring event is so obvious that it demands attention!
Does my organisation really want to prevent the event happening again?
This sounds like a ridiculous question but in order for your RCA investigation to be effective you organisation has to “want” to know the answer. If you are running RCA investigations because you are expected to then you will not have the appetite or drive to properly implement the outcomes or to sustain the RCA process itself.
Have we documented the basic characteristics of our RCA process in a simple procedure?
Processes don’t fail due to the lack of a 100 page manual! What is often found however is that repeatable, sustainable processes have supporting documentation that covers the processes basic core features. Don’t write massive manuals; just make sure you capture the decisions and characteristics of your process.
If you are able to create a simple, sustainable and repeatable process then you next need to consider how you are resourcing it.
Tip 2: Ensure your RCA process is appropriately resourced
It’s easy to think that a good outcome can be obtained by assigning a good person to each RCA investigation. In reality it takes much more than a couple of good people to make your RCA process effective. Even the best investigator will struggle to achieve anything meaningful if they are not correctly resourced and supported. Ask yourself the following questions:
Have we trained the correct people?
You may have people in your team that are natural investigators. These are the ones that just breathe the level of diligence, attention to detail and unbiased approach that all good investigators need. In some cases these people need very little training and can adapt themselves to any RCA tool or process they are asked to use. On the other end of the scale you may also have people that just don’t seem suited to investigative work. They are the ones that will never be able to run an RCA investigation, no matter how much training they have.
In the middle is the other 95% of your team. This is the group that will benefit from dedicated RCA training, helping them to increase their contribution to RCA investigations. Make sure you are running enough training to keep you people improving and refreshed.
Are we setting the correct timeframes for RCA investigations to be done well?
One of the biggest resources that an RCA investigation needs is time. If you give too little time then you are in danger of rushing to an outcome. If you set too much time then the sense of urgency dissipates and you may lose the drive needed to arrive at a quality outcome. Each RCA investigation should be set timeframes based on its assumed complexity and business value.
Have we made the required facilities available?
According to its complexity, consider setting up a “War Room” or “HQ”. It will give the team somewhere to spread out and call home, as well as a sense of visibility to those around them. It also helps to define the importance of the timeframe for each RCA investigation when someone highlights, “We have assigned this meeting room to you for 2 weeks.”
Do we have the right equipment?
Have you given the team access to the right equipment? Cameras and other information gathering tools are vital and an important tool in any investigation. Computer access also plays a big part in how an RCA investigation develops.
Do we have access to the right people?
Make sure you choose the right person to lead each RCA investigation, not just the most available person. If the RCA appears to revolve around mechanical issues then make sure someone with mechanical skills is available to assist.
Also make sure that issues are investigated across teams. Don’t always put the operations superintendent in charge on an RCA investigation that appears to involve operator error. Bringing in other skills and alternative viewpoints can dramatically increase the impartiality and effectiveness of each investigation.
Do we have the right information?
Did anyone think to check that you are investigating the right event? The first task for any RCA investigation should be to establish the details of the actual event. Well before you can establish “why” something happened you need to establish “what” actually happened. Make sure the RCA investigation team has access to the right people, data and locations. This will help them to collect data and verify both the actual events and the root causes behind them.
Part of the setup and resourcing of an effective RCA investigation is the understanding that it is not a solo event.
Tip 3: Make sure RCA investigations are a team event not a solo event
It is tempting to allow the person running the RCA investigation to be responsible to drive it as well. This will not work! At some point the investigation it is going to need somebody other than the lead investigator to get behind it. Ask yourself the following questions:
Who is going to provide the information and expertise to fully investigate the event and arrive at the best solutions?
No one person holds all the knowledge and expertise required to satisfactorily investigate most incidents. Expecting the Reliability Engineer to “fly solo” when performing an RCA is asking for suboptimal results. Plant operators, maintainers, procurement, stores, project engineering and others may all need to be involved in the investigation and in the selection of appropriate solutions. You must make sure that they are committed to participating in the process, and are fully and actively engaged in it if you want to achieve the best results.
Who is going to own the outcomes when the investigation is complete?
At the end of every investigation is a list of actions that need to be implemented. Someone has to take accountability for these actions if you want them to get done. If the person responsible for these actions gets their first glimpse of them in the final report then don’t be surprised if they struggle to get implemented. There needs to be a team approach to RCA investigations, one that brings the final owner along on the journey. This can help the RCA team to gauge the appetite for the organisation to implement the suggested changes.
Who is going to help the investigation team overcome roadblocks?
Each RCA team will run up against roadblocks. When this happens it can be very destructive to the quality of the final outcome. Make sure the RCA team has a sponsor with enough influence to overcome the roadblocks that they may face. Make sure the sponsor is kept in the loop as the investigation evolves and develops.
Who is going to add credibility to the outcome of the investigation?
The setting up of a working group is an effective way of increasing the quality and focus on each RCA investigation. The working group may be made up of other trained investigators or it may be an established management team. Their role is to provide an overview of the type of investigations, timing, outcome and quality of implementation. They provide a focus and encouragement to the RCA team as well as being a sounding board for queries.
A working group is a great way of ensuring that the RCA process is sustainable and of sufficient quality to drive improvement within your business. It will however require the working group to understand what a good RCA investigation looks like, which brings us to our next tip.
Tip 4: Learn what a good outcome looks like and expect it
The working group and other key stakeholders need to have a basic understanding of what a “good” investigation looks like.
“He with the most outcomes and actions wins… is not something to aspire to”
If those reviewing the RCA investigation findings don’t know what a good outcome is then you are just “ticking a box”. Ask yourself the following questions:
Are the findings supported by verifiable data?
The findings may match your suspicions but are they verifiable? Do they hold up to scrutiny and review? Your findings should stand on their own, backed by verifiable data. You should also feel quite safe in questioning them: if they are valid they will survive your questioning.
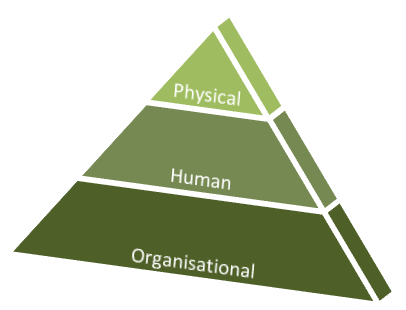
Do we understand the difference between “quick” and “well”?
A quick investigation can help to capitalise on the emotional energy of an event, assisting in getting the actions accepted and implemented. Balance this with the need to do investigations well, not just quickly. Don’t rush an investigation to meet a deadline. If the investigation needs more time the renegotiate the timeline.
An investigation can result in many findings. You may not have the capacity to action a lot of findings so you need to work out which ones are actually root causes and which ones are symptoms. If we focus on the symptoms then we will never prevent the event happening again, or the event will just manifest in a different set of symptoms.
Good quality investigations tend to start at the physical factors, push through the human factors and arrive at the underlying organisational factors that caused the event.
The following example of an incident is used to demonstrate the difference in these factors:
Event:
The team investigating a car rollover found that the wheel had fallen off on the corner, causing the car to lose control and roll over.
Physical Factors:
The rollover was caused by a wheel falling off while the car was turning a corner at speed. This was caused by the wheel nuts coming off on 3 of the 5 wheel studs, in turn causing the remaining 2 studs to snap off.
Human Factors:
The wheel nuts were not tightened correctly by the last person to change the tyre. They also did not check them again once the tyre was changed.
Organisation Factors:
There is no training and competency process for ensuring that people are able to safely change a tyre. There is also no process for checking the quality of safety critical tasks.
In this hypothetical incident addressing the organisational factors will give the best chance of preventing a reoccurrence of the event. Focussing on the physical or human factors will only prevent a reoccurrence of this specific event but will still allow other similar events to occur.
You must push towards the organisational level factors to prevent repeat incidents from happening. Until you solve the root causes at organisation level events are going to repeat themselves, having not solved the underlying root causes of the incidents.
Now comes the hard part, often the most difficult step in an investigation, and one that will destroy the sustainability of your RCA process if neglected.
Tip 5: Follow through each RCA investigation and their outcomes
“The credibility of your next investigation starts with the ability to implement the outcomes of your last one.”
The best way to ensure your process stalls it to ignore the findings from your last RCA investigation and fail to implement them. If you don’t agree with the findings and actions then check to see if your working groups and stakeholders are performing their function. Avoid arriving at the end of an investigation without the appetite to implement the actions!
After a long and complex investigation the lead investigator politely refused to accept the next investigation, stating, “When you show me that you are willing to do something with the findings of the last investigation, I will know you are ready to value the effort I am willing to put into the next one”.
That is a gusty call by the investigator! However this real example brought about a significant change in the management group that was generating the requests for the RCA investigations. It forced the team to engage more in the findings and work to action the outcomes. Ask yourself these questions:
Are we implementing the actions from our RCA investigations?
Track the outstanding actions from your RCA investigations and resource them correctly. The credibility of your RCA process depends on it! Sceptics will be watching from the sidelines, waiting to show that the investment in training and resources has achieved nothing. Don’t give them an easy win! Are we measuring the success of our RCA investigations? The end result of an RCA process should be continual business improvement. If you are running RCA investigations on recurring equipment breakdowns then expect to see an improvement in Mean Time Between Failure (MTBF) and availability of the equipment. If you are running RCA investigations on recurring safety events then expect to see a reduction in these events. If you are not seeing the corresponding reduction in the events that you are investigating then review the findings and see if you are actually getting to the root causes. If you are not even measuring this then how are you going to know that your RCA process is working?
No matter what process you have established, success will only come if you support it and drive it, relentlessly. These tips are not impossible to achieve, they will however require an investment in your process and a consistent pursuit of improvement.
Which of these 5 tips are you struggling to apply? Do you need help in taking your RCA process from a good looking process to a process that actually produces results?
We have experience across all of the concepts discussed in this article. If you feel you need assistance then we can provide experienced consultants and effective training that can help you to dramatically improve the effectiveness of your RCA process. If you would like to take up this opportunity, please contact us.
-
Product on saleRoot Cause Analysis for Team MembersOriginal price was: $2,150.00.$1,935.00Current price is: $1,935.00.
-
Product on saleReliability Excellence FundamentalsOriginal price was: $4,795.00.$4,315.50Current price is: $4,315.50.