As consultants we are not only in a good position to transfer knowledge to our clients, but we are also in a good position to observe and learn from our clients. Although we see many good practices at various clients, these practices often do not always represent good practice for other clients due to their organisational structures and operating context. Good practices might not always translate well between different operations; however, we do identify certain key traits at those clients who deliver effective maintenance practices that could likely be applied to your organisation.
Common traits
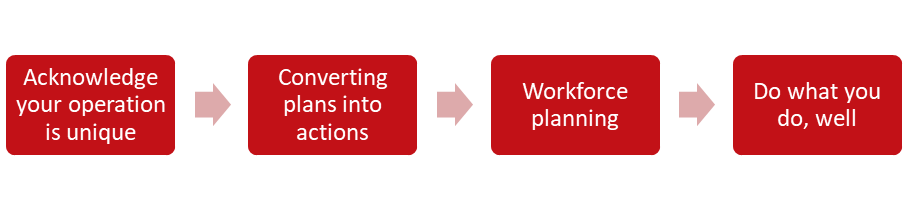
There are various dimensions and good practices that can be identified and discussed, but in terms of my personal experience, these are some of my observations of common traits in effective maintenance delivering organisations:
- Acknowledge your operation is unique – They take the time to ensure that maintenance strategies are suited to their asset application and operating context.
- Converting plans into actions – A simple to follow work management process that aligns with enablers and tools is used to manage delivery of those maintenance strategies to the hands of work execution teams.
- Workforce planning – They understand the resource demand created by the maintenance strategies (and subsequent corrective work) and have clear decision-making criteria on how those resources will be acquired.
- Do what you do, well – Competence and training are targeted in line with objectives, and risks to those objectives, and is seen as adding value to reaching asset performance objectives!
Acknowledge your operation is unique
Organisations that get results from their maintenance strategies understand that no two operations are the same. OEM recommendations offer a fair starting point for how our assets should be maintained, but too often these recommendations are not aligned with the organisation’s operating context and operating profiles.
Further, these organisations accept that time and resources will be required to develop, review and also improve the maintenance strategies. Developing maintenance strategies may not require full time resources and is often a candidate for outsourcing. When outsourcing maintenance strategy development, it is important for specialists to engage with site subject matter experts to capture the operational impacts and requirements that shape how equipment is operated and maintained.
This does not necessarily mean that all assets require the same amount of rigour during maintenance strategy development. These organisations understand the criticality of each asset, the risks to achieving objectives and targets, and subsequently the effort applied to developing those maintenance strategies correlate to the criticality of the asset. Less critical assets often only have OEM recommended strategies or even low value, high volume service contracts.
Converting plans into actions
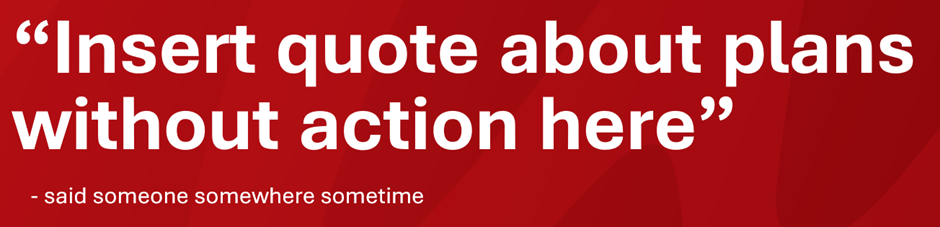
The quote of your choice about “plans without actions” holds true for our best maintenance strategy intentions. Without a structured work management process to deliver maintenance strategies into the hands of those that need to execute them all the maintenance strategy development effort will have been for nothing.
Naturally the work management process should also support management of the corrective follow-up work identified during execution of the maintenance strategies, as well as the failure and immediate work requirements.
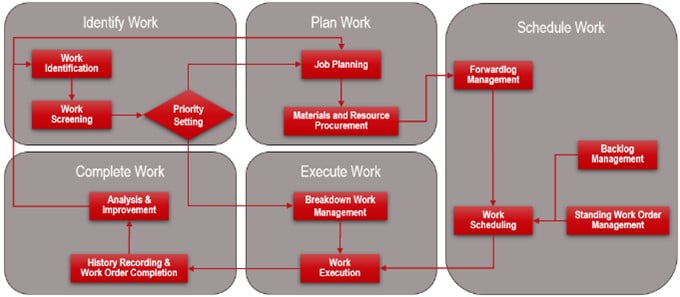
Work may often be deferred, but the key is to stay on top of what is the most important work to be executed.
Again, organisations that do this well have a good understanding of asset criticality and the risks to achieving objectives and targets. This is supported by a culture that promotes open and frequent communication of priorities throughout all levels of the organisation.
Organisations that do work management effectively also demonstrate functional alignment of the work management business processes and the tools (CMMS, EAMS, Mobility etc.) that support it. We have previously discussed functional alignment of process and tools in the following article Getting the most value from your CMMS | Assetivity.
Workforce Planning
The optimal mix of maintenance strategies are likely to require a range of skills that will comprise of general skills like electricians and fitters to specialist skills like structural engineers for instance. Organisations that manage this well determine the organisational skills requirement based on the long-term schedule from their work management process.
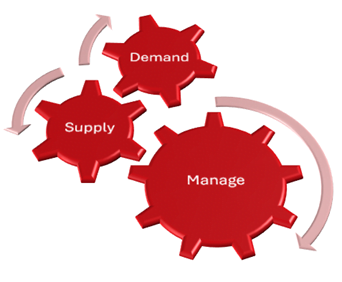
A workforce plan is developed that feeds resource management processes to determine which skills and trades will be maintained and developed in-house, which skills will be outsourced that may include basic service procurement to formally managed contracts and even strategic partnerships.
Risks are identified and managed with regards to scarce skills, or shared resources, which are often coordinated with other organisations. You can imagine the pressure on availability of contractors and skills if all the mines in a certain region decided to do their shutdown maintenance at the same time.
Do what you do, well.
Effective Maintenance organisations identify workforce competences that are essential for success, and proactively ensure that competence is developed and maintained in these areas. This is an area that most organisations struggle with as they often rely on an individual’s own identification of training they want or only focus on basic work-safe training.
Referring to our first theme “Acknowledge your operation is unique”, the same is true for the competence required to maintain your operation. It is simply not enough to assume that each trade person that we have employed is familiar with the types of assets our operations use or that they interpret the work order instructions we give them correctly.
As a practical example from my own operational experience in the mining industry, we found that the opportunity for improvement (or risk to objective) at our multi-site operation was identified by the breakdown cost and labour hours spent on augers, bucket elevators and conveyors. Analysing the opportunity confirmed that the maintenance strategies were correct, the work management process was working efficiently, there was enough labour to execute the work, but the execution was not delivering the results required.
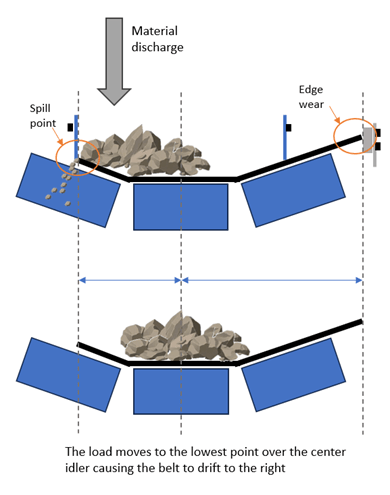
Unfortunately, the work order instructions were not being followed or interpreted as we expected. In this case an in-house competence framework was developed that used the work order instructions as starting point for developing training modules on maintaining the auger, bucket elevator and conveyor. Modules consisted of theoretical learning guides, knowledge questions, model answers and practical tutorials. The initiative also included construction of a small training facility that had an auger, bucket elevator and conveyor for practical tutorials and simulated on the job training.
This training was seen as a crucial risk (risk to objective) mitigation action and when financial pressures warranted reworking the budget, this targeted training would not be subject to budget cuts, unlike what is often seen with training budgets.
In conclusion
There are a multitude of factors to consider when assessing maintenance improvement opportunities in your organisation, especially around the physical factors of the assets you are operating. Hopefully this article has helped to make you aware of some of the softer considerations that also need to be included as part of effective maintenance delivery.
If you need assistance with assessing the current position of your maintenance practices, development of maintenance strategies or work management process improvement, contact one of our experienced consultants today.