Abstract A large mine site was experiencing significant delays in performing planned and preventive maintenance due to unavailability of the required spare parts. This was impacting on equipment availability and reliability. The supply function was being blamed for this situation. The supply function, in turn, blamed Maintenance for failings on its side that, they believed, were preventing Supply from meeting Maintenance’s expectations. An intractable impasse developed over time.
Assetivity was engaged to assist in resolving this situation. This paper will present the approach that was taken and the key lessons learned that will assist any organisation in a similar situation.
Keywords: Supply, Maintenance, Procurement, Stores, Warehouse, Spare Parts
1 Introduction
Many planned maintenance activities for the mobile fleet at a large mine site were being delayed due to spare parts not being available at the desired time for performance of those activities. This, in turn, was contributing to lower than desirable equipment reliability and availability. The mine site had attempted to resolve this issue itself, however passions were running high, and Assetivity was engaged, as an independent third party, to lead a cross-functional, collaborative project, involving both Maintenance and Supply personnel, with the focus being on jointly identifying and addressing the underlying systemic causes that were contributing to this situation. The mine site is located in a remote area, and delivery lead times to that location were long, making effective spare parts and inventory management a critical activity for business success.
2 The Approach Taken
The key to success in this improvement exercise was in gaining consensus regarding the outcomes, and thereby gaining commitment to the resulting action plan.
This was achieved by:
- An objective approach, based on a solid knowledge of Maintenance and Supply best practices, and objective performance benchmarks.
- Creating a non-judgemental environment, in which there were no “winners” and “losers”, merely a joint desire to achieve the best possible performance.
- An open and collaborative approach to the review, with key stakeholders being involved throughout the engagement, so that there are “no surprises”.
- A participative approach in developing agreed actions resulting from the review.
The scope of the project was limited to considering the planning, scheduling and execution of planned and preventive maintenance activities, and the associated supply chain activities to ensure that parts were available to support timely execution of those activities only. This included the conduct of major equipment overhauls and planned component replacement (PCR) activities, but excluded work associated with the conduct of breakdown and unplanned maintenance.
A project team was formed for this project which consisted of:
- A senior representative from the client’s head office Maintenance Support function
- A senior representative from the client’s site Procurement Team
- Two experienced Assetivity consultants
This team was guided by a Project Lead Team, which included:
- The Head of Asset Management for the organisation (from Head Office)
- The Site Maintenance Manager
- The Senior Inventory and Supply Lead
- Principal – Contracts & Sourcing
- Site Superintendent – Supply
- Superintendent – Fleet Engineering
- Site Senior Maintenance Specialist
The approach taken commenced with offsite interviews and data analysis to identify and prioritise the main contributing factors. This then led to a targeted on-site assessment which included a series of on-site discussions, inspection of available facilities, observation of current practices, as well as additional data analysis.
As far as reasonably practicable, all findings and resulting recommendations were substantiated by supporting data and evidence.
3 Key Findings
The study found that a total of 23 factors were contributing to spare parts not being available for planned work at the desired time of maintenance execution. Some of these factors were within the ability of the Supply Function to control, others were as a result of Maintenance processes and actions. Yet others resulted from poor coordination between Maintenance and Supply.
In the interests of space and time, this paper will not detail all 23 findings, but will focus on those that were of greatest significance, and which are more likely to occur at other organisations.
These include the following.
3.1 Over Reliance on Automation and Technology by the Supply Function
The organisation utilised Oniqua (now IBM Maximo MRO) to recommend spare parts holdings by analysing, in near real-time, past procurements and inventory movements. Any recommendations for minimum and maximum spare parts holdings were accepted by the Supply function with little challenge, and without consulting with the Maintenance function. There was little understanding within the Supply function regarding how the algorithms contained within Oniqua worked, and therefore a low level of understanding of any potential weaknesses associated with the use of this software for this purpose.
Because Oniqua relies heavily on past data for its analysis, unless manual intervention is taken, its recommendations assume that past data (for example, relating to the level of demand for a spare part, or the expected delivery lead time) is representative of the future. For the most part, the Oniqua recommended holdings were appropriate in situations where parts demand was constant, and sufficient past data was available to be able to rely on its accuracy. For this particular mining company, however, in most situations this was not true.
Maintenance workload, and therefore the demand for spare parts had been steadily increasing over the previous 3 years, as illustrated in as the mining fleet became older and less reliable as indicated in Figure 1 below. This was due to two main factors, both well-known and highly predictable:
- As the mine went deeper, additional mining equipment was required to be operated in order to maintain mine output.
- As the fleet aged, it was becoming less reliable and more maintenance-intensive.
To support this increase in workload, additional spare parts holdings were required. Oniqua detected this, however because its algorithms were based on past demand, rather than forecast future demand, there was a lag in updating the recommended spare parts holdings that was contributing to stockouts of some critical items.
As mentioned earlier, however, these two contributing factors were well known by the Maintenance department, and if there had been a higher level of cooperation and coordination between the two functions, these stockouts could have been avoided.
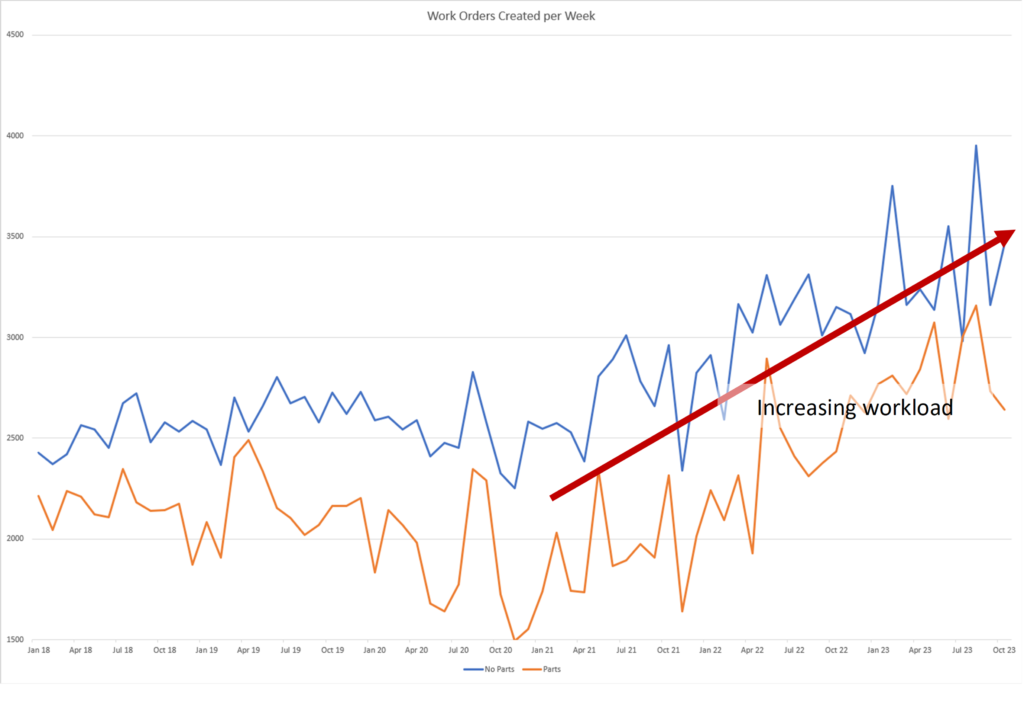
Figure 1 – Maintenance Work Order Volume by Month
Another example of over-reliance on automation and technology related to the processing of Vendor-held inventory (VHI). A key supplier held spare parts inventory on site, and when a work order was released which required VHI materials, a Purchase Order for that material was automatically generated and issued to the vendor within 15 minutes. When the Purchase Order delivery date came due a batch job automatically generated the relevant goods receipts and invoices, with no manual verification prior to this process occurring. This automated process assumed that all materials required from VHI would be available to be issued at the specified delivery date. It also assumed that there would be no processing errors on the part of the vendor. This was resulting in situations where, according to the client’s systems, work orders had been fully provisioned with the required VHI parts, but in fact this was not the case. As a result, when Maintenance came to execute the work order at its scheduled time, they would find that not all materials were available.
3.2 Issues with Maintenance Planning and Scheduling
There were several issues relating to the processes associated with planning and scheduling maintenance work, and the quality with which this work was performed. These included the following:
- The planners who were scoping the maintenance work to be done were not qualified tradespeople, and in most cases did not come from a technical background. This was a deliberate choice by the maintenance function, human resources and finance in order to reduce labour costs. However, in some circumstances, this led to poor quality planning, and in particular, a failure to identify all of the materials required in order to complete a maintenance work order.
- This above issue was compounded by the fact that, if parts were added to a work order after it had been released, the requirement for these additional parts was not automatically communicated to the supply function. If these additional parts needed to be ordered on demand, or if the reservation of these additional parts would lead to stock levels falling below the reorder point, these parts would not be ordered. The absence of these parts would only be detected shortly before the work was due to commence.
- Another challenge that existed relating to Planning and Scheduling was the inability, on the part of the planners and schedulers, to have visibility of current or future forecast stock levels for Vendor-held Inventory. VHI was controlled in the vendor’s information system, and site planners and schedulers did not have access to this system. As a result, an assumption was made that all VHI materials would be available on the delivery date specified on the Purchase Order. In practice, this was not always the case, and stockouts occurred as a result. Once again, the absence of these parts would only be detected shortly before the work was due to commence, leading to a need to reschedule the maintenance work, even though most parts for the work order had already been issued.
- Another limitation of the ERP software that was being used was that the delivery date for VHI was locked in at the time that the work order was first released. The delivery date could not be altered without manual intervention and direct communication with the vendor. The consequences of this were that if a work order was rescheduled to be completed earlier than when first scheduled, VHI parts would not be issued for that work order without manual intervention. In the situation where a work order was reschedule to be performed later than originally intended, unless the Maintenance Scheduler contacted the vendor directly, the VHI parts for that work order would still be issued on the original scheduled date, leading to a build up of inventory in the Kitting and Staging area (which we will discuss later). Unfortunately, many of the schedulers working within the Maintenance function were unaware of this limitation of the ERP, and so the necessary communication with the vendor rarely happened.
- Similarly, maintenance planners and schedulers were sometimes unaware of the lead time limitations imposed on the supply function as a result of its lengthy supply chain. This led to some planned work orders being scheduled for a time period within which work could not realistically be performed, given the existing knowledge regarding parts availability and spare parts delivery lead times.
3.3 Issues with Expediting and Issue Resolution
There were no proactive processes in place within the Supply Function to proactively identify:
- Overdue purchase orders,
- Materials that were at risk of not being available by the required issue date, or
- Materials that had not been received by the required delivery date.
As a result, Maintenance was left with the task of addressing these issues, typically only after the work had been scheduled for execution. However, accountabilities for dealing with these issues were unclear, there were no documented processes for dealing with these issues, and the boundaries between Maintenance and Supply when dealing with these issues were equally unclear. As a result, most of the time work orders which were unable to be performed at their originally scheduled time were simply rescheduled to a future date assuming that the issues would be resolved by that date, but with nobody actually working on resolving the issues this quickly led to a vicious cycle of ongoing rescheduling.
3.4 Kitting and Staging
It is not uncommon (in fact it is good practice) to kit and stage parts shortly prior to execution of the work order for which they are required. Most often this is performed by the Supply function.
However, at this particular mine site, the Maintenance function had a very low level of trust in the Supply function’s capability to ensure that parts would be available in full at the required time. This was at least in part due to the issues mentioned earlier in this paper. As a result, the Maintenance function controlled the Kitting and Staging area. There were several issues associated with this.
The process for kitting and staging involved maintenance personnel working within the kitting and staging area involved:
- Receiving materials either from Vendor-held Inventory or the mine’s own spare parts warehouse
- Tagging these items with the relevant work order number
- Printing the required parts list for each work order and attaching it to the relevant bins – one or more parts bins were used per work order.
- Using the printed parts list to indicate the parts that have been added to each bin and updating the bin location in the ERP system.
- Storing the parts bins on undercover shelving within the Kitting and Staging Area. Larger items that did not fit within the bins were labelled and stored in a separate area that was mostly uncovered.
- Once all parts required for a work order had been verified as being present, the ERP system was updated to indicate that all parts had been confirmed and that the work order is ready for scheduling.
- As a final step the bin was zip-tied to indicate that the bin contained all the parts required.
Note that work orders are only scheduled for execution once all parts had been physically verified as being present. This led to at least a two-week gap between the parts being physically present, and the work being executed. In addition, because of this and the other issues mentioned earlier, there was a large number of parts being stored in the kitting and staging area that were either overdue for execution or were not scheduled to be executed for some considerable period of time (in one case, parts were being stored for a work order that was not scheduled to be performed until 2029). This is illustrated in Figure 2 below.
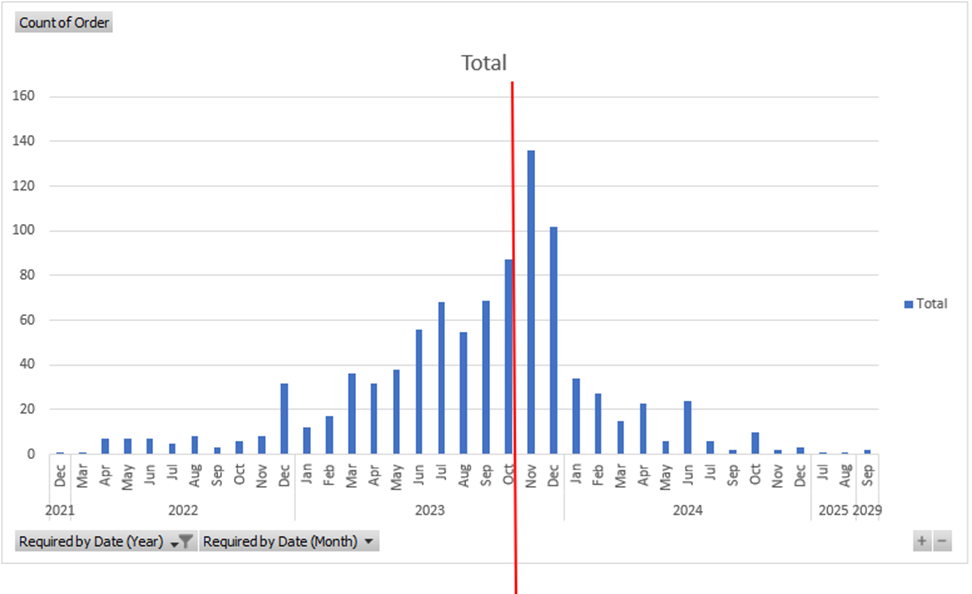
Figure 2 – Parts issued versus Required by Date |
However, the area being used for kitting and staging was not physically secured. Anyone could readily access this area, and many people did. As a result, if a mechanic found that they needed an extra part to complete a planned work order, or to perform breakdown or unplanned work, the kitting and staging area was seen as being an attractive place to start looking for parts. A stocktake of a sample of bins indicated that at least 10% of the bins that had been marked as containing all the parts required for the work order for which it had been allocated had parts missing. Furthermore, nobody was chasing up these missing parts.
All of this led to overcrowding within the Kitting and Staging Area, with parts being damaged as a result of being stored in unacceptable conditions – often in the open air – and with no form of parts care being undertaken. See Figure 3 below. On occasions, parts had to be scrapped and reordered as a result of being in such a poor condition that they could not be installed. In other situations, poor quality parts were used, with the resulting knock-on effect of low equipment reliability.
Low equipment reliability led to an increase in the amount of unplanned maintenance. To source the parts for this unplanned maintenance, parts were frequently “robbed” from future planned work orders. However, no process was in place to inform Supply that these parts needed to be re-issued or reordered.
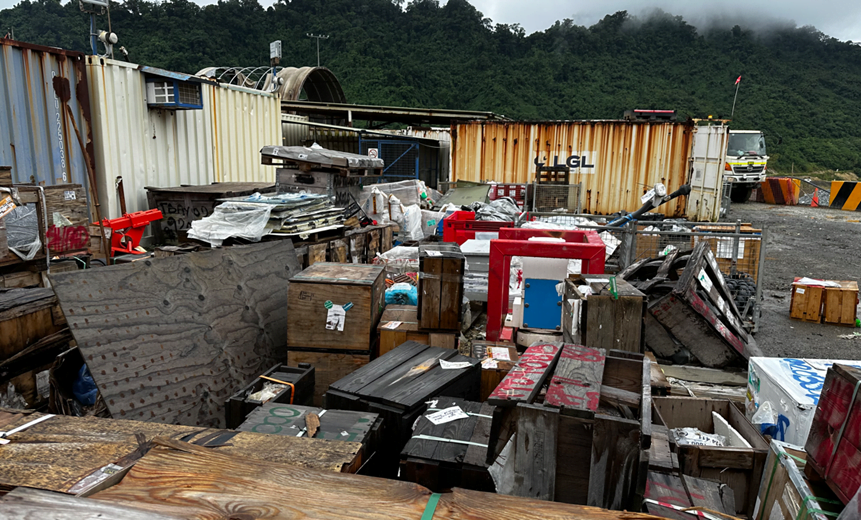
Figure 3 – Spare Parts storage conditions
Furthermore, when assessing the volumes of transactions passing through the kitting and staging area, and comparing this with benchmark levels of store person productivity, the kitting and staging area was significantly undermanned. This, in turn led to significant backlog of materials that had been received by the kitting and staging area but were yet to be processed. This led to a significant number of work orders being listed as not yet being ready to be scheduled, even though all parts had, in fact, been received in the kitting and staging areas.
In addition, when doing a spot check of the storage bins we found a number of bins which contained all of the parts required for execution of the work order, but where the work order status had not been updated to ready within the ERP system. No process was in place to follow up on the parts status for work orders which were overdue due to lack of parts, and so these work orders were stuck in a loop where they were continuously being rescheduled to a future date – even though those work orders could have been executed.
4 Conclusion
In combination, all of the issues described above was contributing to an ever-increasing vicious cycle where more and more parts were unavailable when required, which in turn was leading to ever-reducing equipment reliability, . The finger-pointing and blame-game that existed between Supply and Maintenance was doing little to alleviate the problem.
It was only through objective assessment of the data and the evidence that the solutions to these issues could be identified and implemented. And, in many cases, the solutions lay not just in addressing the issues that existed within the Maintenance function or within the Supply function, but in addressing the communication and coordination gap that existed between these two departments.
[1] Sandy Dunn (*)
Managing Director, Assetivity, Perth, Western Australia
e-mail: sandy.dunn@assetivity.com.au